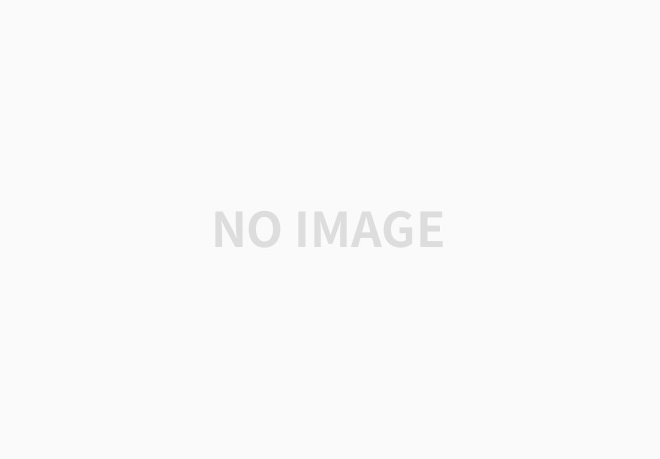
o 관련규격 및 자료
- ASME SEC. Ⅸ : Welding and brazing qualification (2013)
- ASME SEC. Ⅷ : Rules for Construction of Pressure vessels (2013)
- KS B 6750 압력용기설계 및 제조일반 (2012)
- KS B 6751 압력용기 용접일반 (2012)
o 관련법규․ 규칙․ 고시 등
- 산업안전보건기준에 관한 규칙 제2편 제2장 제4절(화학설비·압력용기 등)
압력용기의 용접설계에 관한 기술지침(M-111-2015)
1. 목적
2. 적용범위
3. 용어의 정의
4. 용접이음 설계 시 고려사항
5. 용접설계 및 제작
6. 시험 및 검사
1. 목적
이 지침은 산업안전보건기준에관한 규칙(이하 “안전보건규칙”이라 한다) 제2편 제2장 제4절 (화학설비·압력용기 등) 의 규정에 따라 압력용기를 안전하게 제작하기 위하여 용접설계시 반영하여야 할 일반적인 사항을 제시하는데 목적이 있다.
2. 적용범위
이 지침은 20MPa 이하로 설계된 탑조류(Tower 또는 Column), 용기(Vessel), 열교환기(Heat exchanger) 등의 압력용기 용접설계에 관하여 적용한다.
3. 용어의 정의
(1) 이 지침에서 사용하는 용어의 정의는 다음과 같다.
(가) 압력용기(Pressure vessel)”라 함은 용기의 내면 또는 외면에서 일정한 유체의 압력을 받는 밀폐된 용기를 말한다.
(나) 안전율(Safety factor)”이라 함은 용착부 재료의 강도(인장강도 또는 전단강도)를 허용응력으로 나눈값을 말한다.
(다) “허용응력(Allowable stress)”이라 함은 용접이음부가 안전하게 유지되는 범위이내에서 허용되는 최대응력을 말한다.
(라) “방사선투과시험(Radiographic test)”이라 함은 방사선을 사용하여 용접부의 내부결함을 조사하는 비파괴시험을 말한다.
(마) “열응력(Thermal stress)”이라 함은 용접시에 반복되는 열에 의해서 모재 및 용착금속 내부에 발생하는 응력을 말한다.
(바) “피로(Fatigue)”라 함은 재료에 반복응력이 가해질 때, 재료의 강도가 저하하는 현상을 말한다.
(사) “이음효율(Joint efficiency)”이라 함은 용접이음부의 건전성을 나타내기 위하여 방사선투과시험의 정도에 따라 모재 두께에 대한 이음부의 두께 효율을 말한다.
(2) 그 밖에 이 지침에서 사용하는 용어의 정의는 이 지침에 특별한 규정이 있는 경우를 제외하고는 산업안전보건법, 같은 법 시행령, 같은 법 시행 규칙, 산업안전보건기준에 관한 규칙 및 고용노동부 고시에서 정하는 바에 의한다.
4. 용접이음 설계 시 고려사항
용접 압력용기를 설계할 때에는 다음 사항을 고려하여야 한다.
4.1 일반사항
(1) 가능한 아래보기 용접이 되도록 한다.
(2) 용접이음형상에는 많은 종류가 있으므로 그 특성을 잘 이해하여 선택한다.
(3) 용접하기 쉽도록 설계해야 한다.
(4) 용접이음이 한 곳에 집중되지 않도록 한다.
(5) 맞대기 용접에서 용접 그루브의 치수와 형상은 완전한 용융과 완전 용입이 가능하도록 설계되어야 한다.
(6) 결함이 생기기 쉬운 용접이음은 피해야 하며 필릿용접 이음은 노즐, 보강재, 기타 일부에 적용 한다.
(7) 압력용기 제작자는 용접에 앞서 용접이음마다 용접시공 절차서를 작성하고 그 절차서에 의한 용접방법 및 조건에 따라 용접이음 설계 및 용접시공 방법의 확인시험을 하여야 한다.
4.2 안전율
(1) 모재 및 용착금속의 기계적 성질(항복점, 인장강도 및 연신, 압축 및 충격치)
(2) 시공조건(용접공의 기능정도, 용접방법, 용접자세, 이음의 종류와 형상, 작업장소, 용접 후 열처리관계, 비파괴시험의 유무 등)의 적부
(3) 사용조건(사용온도, 치사적 물질 및 부식성 등)
(4) 하중의 종류(정하중, 동하중, 진동하중)
4.3 사용의 제한
다음의 용접 이음부는 전 길이에 대한 방사선 투과시험을 실시하여야 한다.
(1) 치사적 물질을 포함하는 압력용기의 동체 및 경판의 모든 맞대기 용접부 (“치사적 물질”이란 「산업안전보건법 시행규칙」 별표11의2 (유해인자 분류기준)에서 정한 급성 독성 물질을 말한다)
(2) 용접 이음부에서 공칭두께가 38㎜를 초과하는 압력용기의 모든 맞대기 용접부
(3) 설계압력이 350kPa을 초과하는 비직화식 증기보일러 동체 및 경판의 모든 맞대기 용접부
(4) 위 (1) 또는 (3)에 따라 전 길이 방사선 투과시험이 요구되는, 압력용기 부분 또는 경판에 부착되는 노즐 및 연결실 등에 있는 모든 맞대기 용접부
(5) 용접이음부 및 부품이 <표1 (a)>에서 허용하는 이음 효율에 기초하여 설계된 압력용기 용접부
5. 용접설계 및 제작
5.1 용접부의 설계
(1) 아크 용접 및 가스용접법에 허용되는 용접 이음부 형식과 각 형식에 허용되는 판의 제한 두께는 <표 1〉 에 따른다.
(2) 연결해야 할 가장자리 치수와 모양은 완전 용융 및 완전 용입될 수 있는 치수와 모양 이어야 한다.
(3) 용접부 두께 차이가 얇은 단면 두께의 ¼ 또는 3㎜ 중에서 작은 값을 초과하는 단면들 사이의 이음부에는 접합단면과 인접표면 사이 오프셋(offset)길이의 3배 이상인 두께 변화부(tapered transition)가 있어야 한다.
(4) 두 단 (course) 이상으로 제조하는 경우 인접단의 길이방향 용접 이음부 중심을 엇갈리게 설치하거나, 두꺼운 판 두께의 5배 이상 분리시켜야 한다.
(5) 겹침 이음부의 경우, 표면 겹침부는 안쪽 판 두께의 4배 이상이어야 한다.
(6) 응력 집중을 감소시키기 위해 필요한 경우 필릿 용접부를 추가하여야 한다.
(7) 용접부에 있는 구멍 또는 인접 구멍
(가) 보강 요건을 충족시키는 임의 형식의 구멍이 용접 이음부에 있어도 된다.
(나) 동체나 경판에 단독으로 있는 개구부로서 보강이 필요하지 않을 경우 범주 B 또는 C의 맞대기 용접 이음부에 있어도 되지만 구멍(길이 중간부에 중심이 있는) 지름의 3배 길이에 대해 방사선투과 시험을 하여 합격하여야 한다.
(8) 압력용기 동체(Shell) 또는 경판(Head)에 부착되는 넥은 완전 용입 홈 용접으로 부착시켜야 한다.
5.2 이음효율(Joint efficiency)
아크 용접 및 가스 용접법에 허용되는 용접 이음부 형식과 각 형식에 허용되는 판의 제한두께와 방사선투과시험 정도에 따른 용접이음의 효율은 <표 1>과 같다.
<표 1> 아크 용접 및 가스 용접 이음부에 대한 최대 허용 이음효율
형식
번호 |
이음부 설명
|
제한 조건
|
이범음주부
|
방사선 투과 시험 정도
|
||
(a)
전 길이 |
(b)
부분 |
(c)
미실시 |
||||
(1)
|
양면 용접 또는 다른 방법으로 완성한 맞대기 이음부. 그 자리에 남겨두는 금속 용접 받침대를 사용하는 용접부는 제외한다.
|
없음.
|
A, B, C, D
|
1
|
0.85
|
0.7
|
(2)
|
위 (1)에 포함된 용접부 이외의 용접 받침대를 사용하는 단면 용접 맞대기 이음부
|
(a) 아래 (b) 외에는 없다.
|
A, B, C, D
|
0.9
|
0.8
|
0.65
|
(b) 한 개 판의 오프셋이 있는 원주 방향 맞대기 이음부.
|
A, B, C
|
0.9
|
0.8
|
0.65
|
||
(3)
|
용접 받침대를 사용하지 않는
단면 용접 맞대기 이음부 |
두께 16㎜ 이하, 바깥지름 600㎜ 이하의 원주 방향 맞대기 이음부에 한한다.
|
A, B, C
|
해당
없음 |
해당
없음 |
0.6
|
(4)
|
양면 완전 필릿 겹침 이음부
|
(a) 두께 10㎜ 이하 길이 방향 이음부
|
A
|
해당
없음 |
해당
없음 |
0.55
|
(b) 두께 16㎜ 이하 원주 방향 이음부
|
B 및 C
|
해당
없음 |
해당
없음 |
0.55
|
||
(5)
|
플러그 용접부가 있는 단면 완전 필릿 겹침 이음부
|
(a) 바깥지름 600㎜를 초과 하지 않는 경판을 두께 13㎜이하의 동체
에 부착 시키기 위한 원주 방향 이음부 |
B
|
해당
없음 |
해당
없음 |
0.5
|
(b) 플러그 용접부 중심에 서 판 가장자리까지의 거리가 그 플러그용
구멍 지름의 1½배 이상인 경우, 공칭 두께 16㎜이하인 재킷을 동체에부착시키기 위한 원주 방향 이음부 |
C
|
해당
없음 |
해당
없음 |
0.5
|
||
(6)
|
플러그 용접부가 없는 단면 완전 필릿 겹침 용접부
|
(a) 동체 내부에 필릿 용접부만 있으며, 요구 두께 16㎜ 이하인 동체에 볼록면이 압력을 받는 경판을 부착시킬
경우 |
A, B
|
해당
없음 |
해당
없음 |
0.45
|
(b) 경판 플랜지의 바깥쪽에만 필릿 용접부가 있으며, 안지름 600㎜
이하 및 요구두께 6㎜ 이하인 동체에 어느 한쪽이 압력을 받는 경판을 부착시킬 경우 |
A, B
|
해당
없음 |
해당
없음 |
0.45
|
<표 2> 범주 A, B, C 및 D 용접 이음부의 대표적 예시

5.3 용접 후 열처리
(1) 용접 구조로 제작하는 용기는 용착금속이나 열영향부의 결함을 방지하고 잔류 응력을 완화할 목적으로 예열, 후열처리 또는 응력제거를 한다. 적용하는 기준은 사용 재료의 종류, 용접방법 및 관련규격에 따라 결정한다. 용접 후 열처리 대상은 <표 2>와 같다.
<표 2> 탄소강 및 저합금강 용접 후 열처리 요건
재 료 | 재 료 두 께(㎜) |
P-No. 1, Gr. No. 1,2,3 P-No. 10C, Gr. No. 1 |
- 공칭두께 38㎜를 초과하는 재료 - 용접하는 동안 최저 95℃ 로 예열하지 않은 공칭두께 32㎜ 초과 38㎜ 이하인 재료 |
P-No. 3 Gr. No. 1,2,3 P-No. 9A, 9B, Gr. No. 1 P-No. 10A, Gr. No. 1 |
- P-No. 3, Gr. No. 3 재료의 모든 두께의 재료 - 공칭두께 16㎜를 초과하는 재료 |
P-No. 4, Gr. No. 1,2 P-No. 5A, 5B, 5C Gr. No. 1 P-No. 15E, Gr. No. 1 P-No. 10B, Gr. No. 1 |
- 원칙적으로 모든 재료 |
재료에 따른 예외 사항 등 기타 사항은 KS B 6750 표 6.5.9(탄소강 및 저합금강의 용접 후 열처리 요건)에 따른다. |
(2) 용접 후 열처리 요건
(가) 용기나 부품을 노에 장입할 때 노의 온도는 425℃ 이하이어야 한다.
(나) 425℃ 초과 온도에서의 가열속도는 222℃ /hr를 동체판 또는 경판의 최대 금속 두께(25㎜ 기준)로 나눈 값 이하이어야 하며, 어떠한 경우에도 222℃ /hr 이하이어야 한다. 가열하는 동안 용기의 가열부위에서 길이 간격 4.6m내에 139℃ 를 초과하는 온도편차가 없어야 한다.
(다) 가열 유지시간동안 용기의 가열부위 전체에 대한 최고 및 최저온도 차는 83℃이하이어야 한다.
(라) 425℃ 초과 온도에서의 냉각은 280℃ /hr를 동체판 또는 경판의 최대 금속두께 (25㎜ 기준)로 나눈 값 이하의 속도로 밀폐된 노 또는 냉각실에서 실시하여야 하며, 어떠한 경우에도 282℃ /hr 이하이어야 한다. 425℃ 부터는 정체된 대기에서 냉각시켜도 된다.
5.4 제작
(1) 이음부의 모양, 치수는 용접시공 절차서에 의해서 정해진 것이어야 한다.
(2) 모재의 온도가 -20℃ 미만인 경우에는 어떤 종류의 용접도 실시하지 않는 것이 바람직하다.
(3) 용접해야 할 표면은 깨끗해야 하고 스케일, 녹, 기름, 유지분, 슬래그, 산화물 및 기타 유해한 이물질이 없어야 한다.
(4) 맞대기 용접을 해야 할 가장자리에서 최대 오프셋(offset)이 해당 용접 이음부 범주에 대한 값을 초과하지 않도록 부재를 정열하여야 한다.
<표 3> 맞대기 용접에서 엇갈림 오차의 허용값
부재 두께 mm | 이음부 범주 mm | |
A | B, C 및 D | |
13 이하 | ¼t | ¼t |
13 초과 19 이하 | 3 | ¼t |
19 초과 38 이하 | 3 | 5 |
38 초과 51 이하 | 3 | ⅛t |
51 초과 | 1/16t 또는 10 중 작은 값 | ⅛t 또는 19 중 작은 값 |
(5) 맞대기 용접 이음부는 완전 용입 및 완전 용융 용접 이어야 한다. 비파괴 시험 결과를 적절하게 해석하기 위하여 용접부 표면에서 거친 파형(ripple), 흠, 겹침부 및 날카로운 돌기와 골을 완전히 제거하여야 하며, 각 면의 용접 덧살은 모재로 부터 매끄럽게 높아져야 하고 그 높이는 다음 <표 4>의 값 이하가 되어야 한다.
<표 4>용접 덧살의 최대 허용 두께
재료의 공칭 두께 mm | 최대 용접 덧살 mm | |
범주 B 및 C 맞대기 용접부 | 기타 용접부 | |
2.4 미만 | 2.4 | 0.8 |
2.4 이상 4.8 이하 | 3.2 | 1.6 |
4.8 초과 13 이하 | 4.0 | 2.4 |
13 초과 25 이하 | 4.8 | 2.4 |
25 초과 51 이하 | 5 | 3.2 |
61 초과 76 이하 | 6 | 4 |
76 초과 102 이하 | 6 | 6 |
102 초과 127 이하 | 6 | 6 |
127 초과 | 8 | 8 |
(6) 필릿 용접을 실시할 경우, 해당 용접부 루트(Root)에서 용접 금속이 모재 속으로 적절하게 용입되도록 용착시켜야 한다.
(7) 양면 용접 이음부의 경우, 용접 금속이 처음 용착된 기초부에 건전한 금속이 나타나도록 반대쪽을 용접하기 전에 뒷면을 치핑, 연삭 또는 용융제거 하여야 한다.
(8) 육안검사, 수압시험 등의 검사를 실시하여 검출한 균열, 핀홀(pinhole), 융합 불량과 같은 결함은 기계적인 방법 또는 열 가우징 방법으로 제거 한 후에 그 이음부를 재용접하여야 한다.
6. 시험 및 검사
6.1 용접절차 확인
승인된 용접 절차서에 따라 용접되었는지 확인하여야 제조자는 해당 요건을 충족시켰음에 대한 증거를 제출하여야 한다.
6.2 용접 후 열처리 작업의 확인
모든 용접 후 열처리의 정확한 실시 및 열처리 온도가 해당요건을 준수하고 있는지 확인하여야 한다.
6.3 기밀시험을 실시할 압력용기
기압시험을 실시 해야하는 압력용기의 경우, 다음 용접부의 전 길이에 대해 균열을 검출하기 위해 비파괴 시험을 실시하여야 한다.
(1) 구멍 둘레에 있는 모든 용접부
(2) 비압력 부품을 압력 부품에 부착시키는 용접부를 포함하여, 목두께가 6㎜를 초과하는 모든 부착 용접부
6.4 용접이음부에 대한 방사선 투과시험
(1) 방사선 투과시험을 실시해야 하는 모든 용접 이음부
(2) <표 1>의 b)열(부분 방사선 투과시험)에서 용접이음효율을 선택한 압력용기 용접부는 15m마다 또는 그 일부에 대해 한 번의 부분 시험(Spot Test)을 실시하여야 한다.
압력용기의 용접설계에 관한 기술지침(M-111-2015)
'산업안전' 카테고리의 다른 글
압력용기 보수에 관한 기술지침(M-113-2012) (0) | 2022.05.14 |
---|---|
배관지지물 설치 및 유지에 관한 기술지침(M-112-2012) (0) | 2022.05.14 |
회전기계의 진동감시 기술기준(M-110-2012) (0) | 2022.04.15 |
압력용기의 두께감소에 따른 위험성평가에 관한 기술지침(M-109-2012) (0) | 2022.04.15 |
배관응력 해석에 관한 기술지침(M-105-2012) (0) | 2022.04.14 |