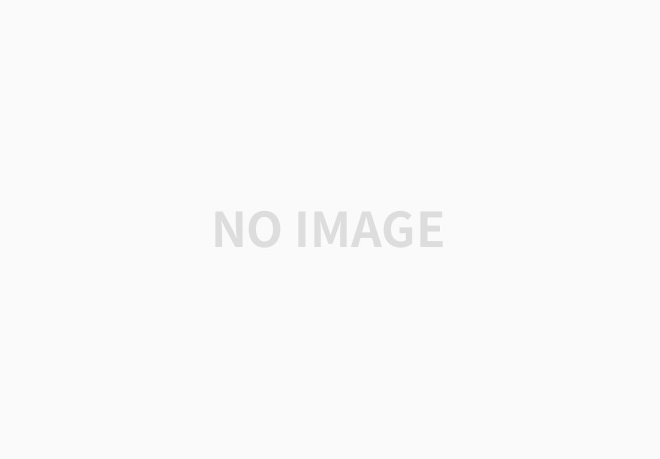
o 관련 규격 및 자료
- KS B 6750 압력용기 - 설계 및 제조 일반 2012.
- KS B 6751 압력용기 - 용접일반 2012.
- ASME Section Ⅷ, Division 1 - “Rules for Construction of Pressure Vessel”, 2012.
- ASME Section Ⅸ, Appendix D P-Number Listing
- ASME B 31.3 Process Piping
o 관련법규·규칙·고시 등
- 산업안전보건법 제34조제1항
- 산업안전보건법 시행령 제28조제1항 제1호
- 고용노동부 고시 제2015-20호 위험기계ㆍ 기구 안전인증 고시
압력용기 용접 후 열처리에 관한 기술지침(M-184-2015)
1. 목적
2. 적용범위
3. 용어의 정의
4. 용접 후 열처리 대상
5. 탄소강 및 저합금강의 용접 후 열처리 요건
6. 비철금속 압력용기 용접 후 열처리
7. 고합금강 압력용기 용접 후 열처리
8. 페라이트계 압력용기 용접 후 열처리
9. 다층(Multipass) 압력용기 용접 후 열처리
10. 저온 압력용기 용접 후 열처리
11. 배관의 열처리
12. 냉간성형되는 압력용기 및 부속품의 용접 후 열처리
13. 고합금강 및 비철금속 압력용기의 변형에 따른 열처리
14. 일반적인 용접 후 열처리 절차
15. 열처리 확인 시험
16. 온도 측정 및 기록
1. 목적
이 지침은 산업안전보건법 제34조제1항 및 산업안전보건법 시행령 제28조제1항 제1호의 규정에 따라 압력용기 및 그 부속설비를 제작 및 수리할 때 잔류응력 등에 의한 잔류응력을 제거하기 위하여 필요한 사항을 정하는데 그 목적이 있다.
2. 적용범위
이 지침은 압력용기 및 그 부속설비, 공정배관을 시공, 제작 및 유지보수 시에 적용한다. 다만, 별도의 열처리 규정이 없는 경우에는 일반기계·기구도 이 규정을 준용할 수 있다.
3. 용어의 정의
(1) 이 지침에서 사용하는 용어의 정의는 다음과 같다.
(가) “후열처리(Postweld heat treatment)”라 함은 용접 및 가열절단 후 조립체에 열을 가하는 퀜칭(Quenching, 담금), 노멀라이징(Normalizing, 불림), 어닐링(Annealing, 소둔, 풀림) 등의 열처리를 말한다.
(나) “예열처리(Preheat treatment)”라 함은 규정 최소 예열온도에 도달할 수 있도록 용접 또는 가스 절단작업을 하기 직전에 모재에 열을 가하는 열처리를 말한다.
(다) “압력용기(Pressure vessel)”라 함은 용기의 내면 또는 외면에서 일정한 유체의 압력을 받는 밀폐된 용기를 말한다.
(라) “주요 구조부분”이란 동체, 경판 및 받침대(새들(Saddle) 및 스커트(Skirt) 등) 등을 말한다.
(마) “공인시험기관”이란 한국인정기구(KOLAS), 국제시험기관인정협력체(ILAC) 또는 아시아태평양시험기관인정협력체(APLAC)에 가입한 인정기구로부터 시험기관 또는 검사기관으로 공인을 받은 기관을 말한다.
(바) “예열(Preheating)”이란 압력용기의 주요 구조부분을 용접 또는 가스절단작업을 하기 직전에 모재가 규정하는 최소 예열온도에 도달할 수 있도록 열을 가하는 작업을 말한다.
(사) “공인검사원”이란 압력용기 관련법에서 검사에 대한 위임 또는 위탁을 받은 공인검사기관에 정식으로 고용된 검사원 또는 해당기관에서 자격을 인정한 사람으로서 압력용기 제조자의 품질관리 시스템의 준수여부를 확인할 의무가 있는 사람을 말한다.
(아) “P-No”란 금속의 화학적 성분과 물리적 성질이 유사한 것을 KS B 6751 압력용기 - 용접일반 2012, ASME Section Ⅸ, Appendix D P-Number Listing에서 분류한 번호를 말한다.
(자) “버터링(Buttering)”이란 육성 덧씌움 용접(Buildup overlay welding)을 말한다.
(2) 기타 이 지침에서 사용하는 용어의 정의는 특별한 규정이 있는 경우를 제외하고는 법, 동법 시행령, 동법 시행규칙 및 안전보건규칙이 정하는 바에 의한다.
4. 용접 후 열처리 대상
(1) 탄소강 또는 저합금강으로 제작하는 치사성 물질 또는 독성물질 취급 압력용기
(2) 탄소강 또는 저합금강으로 제작하는 비직화식 증기 보일러
(3) 직화식 압력용기 또는 부품으로 탄소강(P-No. 1)의 용접이음부 두께가 16 ㎜를 초과하는 경우와 저합금강(P-No. 1의 강 제외)의 모든 용접이음부
(4) 두께 3 ㎜를 초과하는 페라이트계(Ferritic) 재료를 전자빔 용접방법으로 용접할 때 또는 관성 연속 구동 마찰 용접방법으로 임의 두께의 P-No. 3, P-No. 4, P-No. 5A, 5B, 5C, P-No. 10, P-No. 15E의 재료를 용접할 때
(5) 이음부 두께 38 ㎜를 초과하는 페라이트계 재료의 일렉트로슬래그 용접부(Electroslag weld)에 대해서는 결정립 미세화(오스테나이트화(Austenitizing)) 열처리
(6) 38 ㎜를 초과하는 페라이트계 재료의 단일 패스 일렉트로가스 용접부(Electro-gas weld)에 대해서는 결정립 미세화(오스테나이트화) 열처리
(7) P-No. 1 재료에 한해 오스테나이트화 범위에서 다음 5. 탄소강 및 저합금강의 용접 후 열처리 요건에서 (4)의 (나) 또는 (마)의 가열 및 냉각속도에 대한 제약 사항들은 적용되지 않는다.
(8) 배관의 두께가 19 ㎜(3/4 in) 이상인 경우
(9) 탄소강 및 저합금강의 압력용기 동체판 및 경판의 냉간성형으로 제작되는 탄소강판 및 저합금 강판의 압력용기 동체 부분, 경판, 기타 압력경계 부품은 냉간 성형 결과로 최대 연신율(Extreme fiber elongation)이 압연상태를 기준하여 5 %를 초과하고 다음 조건 중의 어느 하나라도 해당하는 경우에는 냉간 성형 이후에 열처리를 하여야 한다
(가) 재료의 충격시험이 요구될 때
(나) 냉간성형 전에 부품의 두께가 16 ㎜를 초과할 때
(다) 최대 연신율(Extreme fiber elongation)이 5 %를 초과하는 곳 어느 곳이든 압연 두께로부터 냉간성형으로 인한 두께 감소가 10 %를 초과할 때
(라) 성형 중 재료 온도가 120 ℃ ~480 ℃ 의 범위일 때
(10) 고합금강 및 비철금속 압력용기의 변경에 기인한 제작 후열처리는 KS B 6750 압력용기-설계 및 제조일반을 참조한다.
5. 탄소강 및 저합금강의 용접 후 열처리 요건
(1) 다음 표 5.1 재료구분과 모재의 종류기호 일람표에서 금지한 경우 외에는, 표 5.2의 최소값을 초과하는 유지온도 및/또는 유지시간을 적용해도 된다.
(2) 중간 용접 후 열처리는 표 5.2 탄소강 및 저합금강의 용접 후 열처리 요건을 준수할 필요가 없다. 표 5.2 탄소강 및 저합금강의 용접 후 열처리 요건에 규정된 온도에서의 유지시간은 연속적일 필요는 없으며, 복수의 용접 후 열처리 주기가 누적된 시간이어도 된다.
(3) P-No. 그룹이 다른 두 압력 부품을 용접 연결할 경우, 높은 용접 후 열처리 온도를 요구하는 재료에 대해 표 5.2 탄소강 및 저합금강의 용접 후 열처리 요건 또는 표 7.1 고합금강의 용접 후 열처리의요건(해당 비고 포함)에서 규정하는 용접 후 열처리를 하여야 한다. 비압력 부품을 압력 부품에 용접할 경우, 압력 부품의 용접 후 열처리 온도를 적용하여야 한다.
표 5.1 재료 구분과 모재의 종류기호 일람표
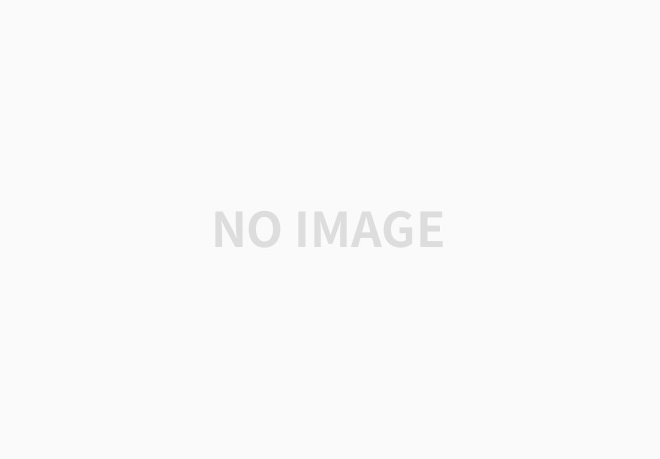
* 출처 : KS B 0954 용접 후 열처리 방법 2012
표 5.2 탄소강 및 저합금강의 용접 후 열처리 요건
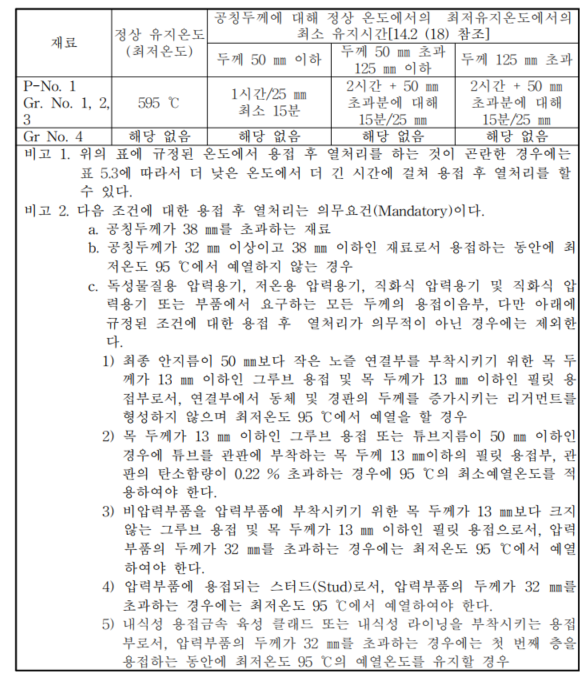
* 출처 : KS B 6750 압력용기 - 설계 및 제조 일반 2012.
표 5.2 탄소강 및 저합금강의 용접 후 열처리 요건(계속)

표 5.2 탄소강 및 저합금강의 용접 후 열처리 요건(계속)
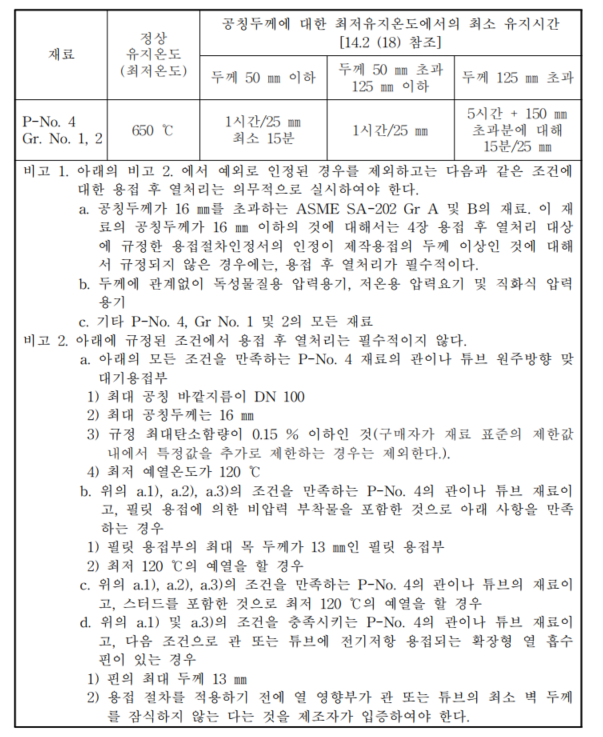
표 5.2 탄소강 및 저합금강의 용접 후 열처리 요건(계속)
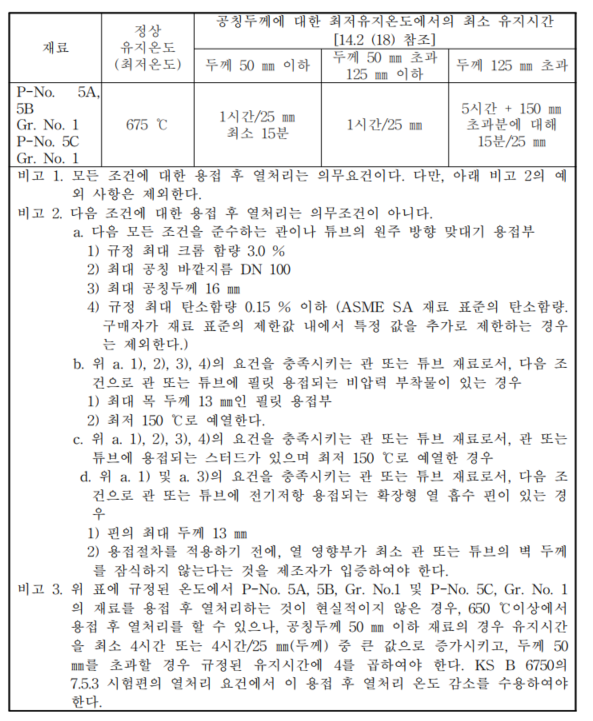
표 5.2 탄소강 및 저합금강의 용접 후 열처리 요건(계속)

표 5.2 탄소강 및 저합금강의 용접 후 열처리 요건(계속)
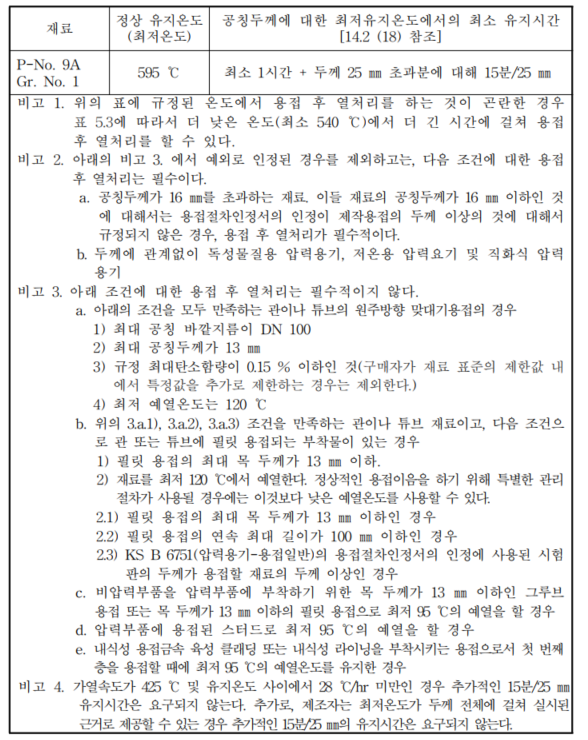
표 5.2 탄소강 및 저합금강의 용접 후 열처리 요건(계속)

표 5.2 탄소강 및 저합금강의 용접 후 열처리 요건(계속)
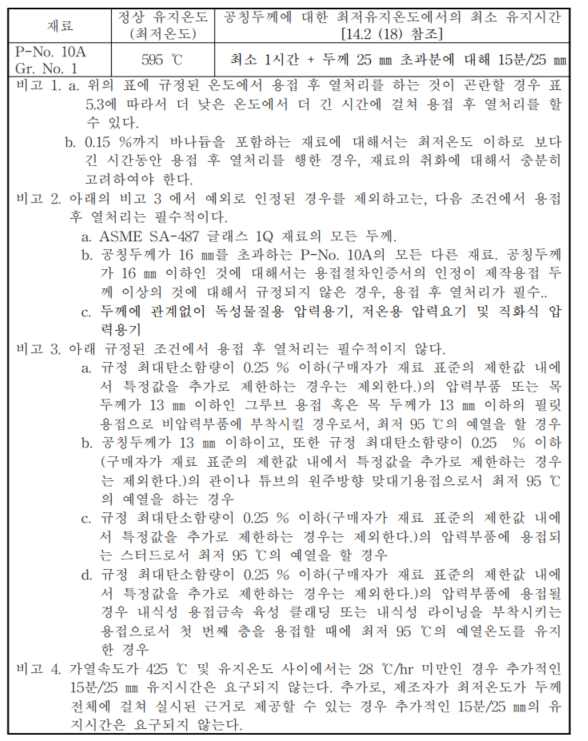
표 5.2 탄소강 및 저합금강의 용접 후 열처리 요건(계속)
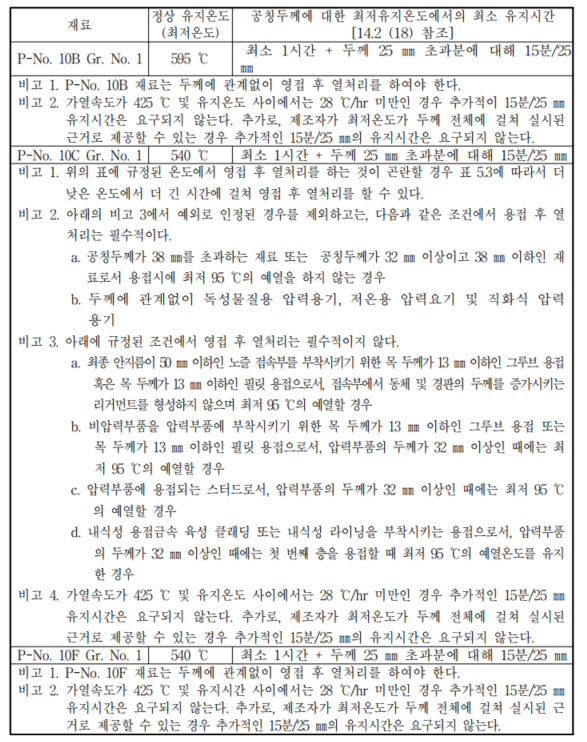
(4) 용접 후 열처리 작업은 다음 요건에 따라 14. 일반적인 후열처리 절차들 중 하나를 적용하여 실시하여야 한다.
(가) 압력용기나 부품을 노에 장입할 때 노의 온도는 425 ℃ 이하이어야 한다.
(나) 425 ℃ 초과 온도에서의 가열속도는 222 ℃ /hr를 동체판 또는 경판의 최대 금속 두께(25 ㎜ 기준)로 나눈 값 이하이어야 하며, 어떠한 경우에도 222 ℃ /hr 이하이어야 한다. 가열하는 동안 압력용기의 가열 부위에서 길이 간격 4.6 m 내에 139 ℃ 를 초과하는 온도 편차가 없어야 한다. 가열 및 냉각속도가 38 ℃ /hr 미만일 필요는 없으나, 밀폐실 및 복잡한 구조물의 경우 과도한 열구배로 인한 구조적 손상을 방지하기 위해 가열 및 냉각속도를 감소시킬 수도 있음을 항상 고려한다.
(다) 압력용기 또는 그 부품은 표 5.2 또는 표 5.3에 규정된 온도 이상에서 이들 표에 규정된 시간 동안 유지되어야 한다. 유지시간 동안 압력용기의 가열 부위 전체에 대한 최고 및 최저 온도 차는 83 ℃ 이하이어야 한다. 다만, 표 5.2에서 이 범위를 제한하는 경우는 제외한다.
표 5.3 탄소강 및 저금강의 용접 후 열처리 요건 대안
최저 규정온도 이하로 감소 (℃ ) | 감소온도에서 최소 유지시간a (hr) | 비 고 |
28 | 2 | - |
56 | 4 | - |
83 | 10 | b |
111 | 20 | b |
a 두께 25 ㎜ 이하에서의 최소유지시간. 두께가 25 ㎜를 초과하는 경우, 25 ㎜ 당 15분을 추가한다. b 낮은 용접 후 열처리 온도는 P-No 1, Gr No 1 및 2 재료에만 허용한다. * 최저 규정온도 미만으로 열처리하는 경우에는 사전에 공인 검사원의 승인을 받아야 한다 |
(라) 가열 및 유지시간 동안 압력용기 표면에 과도한 산화가 발생하지 않도록 노 분위기를 제어하여야 한다. 노는 압력용기에 화염이 직접 닿지 않도록 설계된 노이어야 한다.
(마) 425 ℃ 초과 온도에서의 냉각은 280 ℃ /hr를 동체판 또는 경판의 최대 금속 두께(25 ㎜ 기준)로 나눈 값 이하의 속도로 밀폐된 노 또는 냉각실에서 실시하여야 하며, 어떠한 경우에도 280 ℃ /hr 이하이어야 한다. 425 ℃ 부터는 정체된 대기 중에서 냉각할 수 있다.
(5) 완료된 압력용기 또는 그 부품을 용접 보수한 후에 다시 용접 후 열처리를 실시하고, 공인검사원의 검사를 받아야 한다. 다만, 다음 (6)에서 허용하는 경우는 제외한다.
(6) ① P-No. 1, Gr No. 1, 2 및 3의 재료, ② P-No. 3, Gr No. 1, 2 및 3의 재료 및 ③ 이러한 재료를 연결하는 용접 금속에 대해 최종 공인검사를 실시 후 및 최종 수압시험을 하기 전에 추가 용접 후 열처리를 하지 않고 용접 보수를 해도 된다. 다만, 표 5.3의 예외사항 외에는, 치사성 물질용 압력용기에 따른 사용요건으로 또는 재료결함에 대한 그 보수방법과 범위에 대하여 공인 공인검사원의 승인을 받은 경우는 후열처리를 요구하지 않아도 된다.
(7) 용접 보수는 아래 (가)에서 (사)까지의 요건을 충족시켜야 한다. 용접 보수가 제작용 고정구를 제거한 후에 요구되는 보수와 같이, 재료 표면을 경미하게 복원하는 경우로서 그 표면이 압력용기 저장물에 노출되지 않는다면 이 요건은 적용하지 않는다.
(가) 제조자는 공인검사원 및 사용자에게 해당 보수를 사전에 통보하여야 하고, 승인을 받을 때까지 보수작업을 진행하지 않아야 한다. 이러한 보수는 자료보고서에 기록하여야 한다.
(나) 총 보수 깊이는 P-No. 1, Gr No. 1, 2 및 3의 재료에 대해서는 38 ㎜ 이하 , P-No. 3, Gr No. 1, 2 및 3의 재료에 대해서는 16 ㎜ 이하이어야 한다. 용접 보수의 총 깊이는 해당 위치에서 용접부의 양면에 대해 실시한 보수 깊이의 합으로 결정하여야 한다.
(다) 결함을 제거한 홈에 대해서는 액체침투탐상시험법 또는 자분탐상시험법으로 검사하여야 한다.
(라) 홈 용접부에 대한 용접절차 시방서를 인정하기 위한 KS B 6751의 해당 요건 외에 다음 요건을 추가로 적용하여야 한다.
① 용접금속은 저수소계 용접봉을 사용하여 피복금속 아크 용접방법으로 용착시켜야 한다. 용접봉은 ASME. Sec. Ⅱ , Part C, SFA-5.5, Appendix A6.11의 요건에 따라 적절하게 건조시켜야 한다. 최대 비드 폭은 용접봉 심선 지름의 4배 이어야 한다.
➁ P-No. 1, Gr No. 1, 2 및 3의 재료에 대한 보수 부위는 예열하여야 하며, 용접하는 동안 최저 온도 93 ℃ 를 유지하여야 한다.
➂ P-No. 3, Gr No. 1, 2 및 3의 재료에 대한 보수 용접방법은 반층 비드 용접 보수 및 템퍼비드 용접기법(Weld temper bead reinforcement technique)으로 제한하여야 한다.
➃ 보수 부위는 예열하여야 하며, 용접하는 동안 최저 온도 175 ℃ 를 유지하여야 한다. 층간 최고 온도는 230 ℃ 이어야 한다.
➄ 용접 금속의 첫 층은 최대 지름 3 ㎜의 용접봉을 사용하여 전체 면적에 용착되도록 하여야 한다. 다음 층을 용착시키기 전에 첫 층 두께의 절반을 연삭 제거하여야 한다.
➅ 후속 용접층은 이전 용접 비드 및 열영향부가 템퍼링(Tempering)될 수 있도록 최대 지름 4 ㎜의 용접봉을 사용하여 용착시켜야 한다.
➆ 모재 열영향부의 템퍼링을 보장하기 위해 모재와 접촉하지 않으면서 하부 용접 비드의 가장자리에 충분히 근접하도록 보수된 표면 위의 높이까지 최종 템퍼 비드 용접을 적용하여야 한다.
➇ 모든 용접 완료 후, 보수 부위를 최소 4시간 동안 205 ℃ ~260 ℃ 의 온도로 유지하여야 한다.
➈ 최종 템퍼 비드 용접 덧살층은 모재의 표면과 거의 동일 평면이 되도록 제거하여야 한다.
(마) 완료된 보수 용접부가 대기 온도에 도달한 후, 위 (다)에 적용된 방법과 동일한 비파괴 시험을 실시하여야 한다. 다만, P-No. 3, Gr No. 3의 재료에 대해서는 용접부에서 균열의 지연 발생 여부를 확인하기 위하여 재료를 주위 온도로 최소 48시간 동안 유지한 후 시험을 실시하여야 한다.
(바) 자분탐상시험법으로 시험한다면, 교류 요크법 만이 허용된다. 또한 이 표준에 따라 방사선 투과 시험이 요구되는 재료 및 용접부에서 깊이가 10 ㎜를 초과하는 용접 보수 부위는 KS B 6750의 8.2.6에 따라 방사선투과시험을 실시하여야 한다.
(사) 용접 보수 후에는 압력용기를 수압시험하여야 한다.
(8) 냉간 성형 제작한 동체 부분, 경판 및 다른 압력 경계 부품은 냉간성형으로 인해 압연 상태에서 최대 연신율이 5%를 초과하는 경우, 후속 용접 후 열처리를 하여야 한다. P-No. 1, Gr. No. 1 및 2 재료의 최대 연신율은 다음 조건에 해당하지 않을 경우 40 %까지 허용한다.
(가) 압력용기에 액체 또는 기체 상태의 치사성 물질을 저장하는 경우
(나) 규정에 따라 그 재료를 충격시험에서 면제하지 않았거나, 해당 재료 표준에 따라 충격시험이 요구되는 경우
(다) 냉간 성형하기 전 부품의 두께가 16 ㎜를 초과하는 경우
(라) 최대 연신율 5 %를 초과하는 임의 위치에서 압연 상태에서 냉간 성형에 의한 두께 감소가 10 %를 초과하는 경우
(마) 성형할 때 그 재료의 온도가 120 ∼ 480 ℃ 의 범위에 있을 경우
6. 비철금속 압력용기 용접 후 열처리
(1) 비철금속 재료의 용접 후 열처리는 일반적으로 필요하지 않으며 바람직하지도 않다.
(2) 사용자와 제조자가 합의한 경우 외에는 용접 후 열처리를 하지 않아야 한다. 다만, 아래 (3), (4) 및 (5)는 제외한다. 열처리 온도, 시간 및 방법에 대해서는 합의하여야 한다.
(3) 용접하는 경우, AMSE SB-148 합금 CDA 954의 주조품은 모든 용접 후 620~650℃ 에서 첫 단면 두께 25 ㎜에 대해 1.5시간 동안, 그리고 두께가 25 ㎜ 증가될 때마다 30분씩 추가하여 열처리하여야 한다. 이후 재료를 공랭시켜야 한다.
(4) 용접 후 14일 이내에 지르코늄 등급 R60705의 모든 제품은 540~595 ℃ 에서 두께 25 ㎜까지는 최소 1시간 동안, 그리고 두께가 25 ㎜ 증가될 때마다 30분씩 추가하여 열처리하여야 한다. 425 ℃ 이상에서는 밀폐된 노 또는 냉각실 내에서 냉각시켜야 한다. 이때 냉각속도는 278 ℃/hr 를 동체나 경판의 최대 두께(인치 단위)로 나눈 값 이하이어야 하지만, 278 ℃ /hr를 초과하지는 않아야 한다. 425 ℃ 에서부터 압력용기를 정체된 공기 중에서 냉각시켜도 된다.
(5) UNS N08800, N08810 및 N08811 합금의 용접 후 열처리는 다음과 같이 실시한다.
(가) UNS N08800(alloy 800), N08810(alloy 800H) 및 N08811(alloy 800HT)로 제작한, 설계온도가 540 ℃ 를 초과하는 압력용기의 압력 경계 용접부 및 압력 경계에 대한 부착 용접부는 용접 후 열처리하여야 한다.
(나) 용접 후 열처리는 두께 25 ㎜까지는 최저 885 ℃ 에서 1.5시간 동안, 그리고 두께가 25 ㎜ 증가될 때마다 1시간씩 추가 가열하여야 한다. 냉각 및 가열속도에 대해서는 구매자와 제작자가 합의하여야 한다. 대안으로 해당 재료 표준에 따른 고용화 어닐링을 허용한다.
(다) 튜브-관판 및 확장 벨로우즈 부착 용접부에 대한 용접 후 열처리는 요구하지도 금지하지도 않는다.
(라) 용접 후 열처리된 압력용기 또는 그 부품에 대해서는 용접 보수를 실시한 후 다시 용접 후 열처리하여야 한다. 다만, 아래 (마) ③에서 허용하는 경우는 제외한다.
(마) 이러한 재료를 연결하는 용접부에서 용접 금속 및 열영향부에 대한 용접 보수는 최종 용접 후 열처리 후에 실시하여도 되지만, 최종 수압시험하기 전에 추가용접 후 열처리를 하지 않고 완료하여야 한다. 용접 보수는 아래 ➀∼④ 요건을 충족시켜야 한다.
➀ 제조자는 공인검사원 및 사용자에게 보수에 대해 사전에 통보하여야 하며, 사용자로부터 승인을 받을 때까지 작업을 진행하지 않아야 한다.
➁ 총 보수깊이는 13 ㎜ 또는 재료두께의 30 % 중 작은 값을 초과하지 않아야 한다. 용접 보수의 총 깊이는 해당 위치에서 용접부의 양면에 대해 실시한 보수 깊이의 합으로 결정하여야 한다.
➂ 결함을 제거한 후, 그 홈을 검사하여야 한다. 또한, 용접 보수부위도 검사하여야 하며, 규정에 따라 침투탐상시험을 실시하여야 한다.
➃ 용접 보수 후에는 그 압력용기를 수압시험을 하여야 한다.
(6) 용접부에서 냉간 성형 굽힘 반지름이 해당 구성품 두께의 4배 미만인 경우, UNS R31233의 용접 후 열처리는 냉간 성형을 하기 전에 실시하여야 한다. 용접 후 열처리는 1,121 ℃ 에서 어닐링한 직후 수냉시켜야 한다.
7. 고합금강 압력용기 용접 후 열처리
(1) 고합금강 압력용기에 적용해야 할 용접절차는 공인검사원 조건 또는 면제 조건과 아래에 제시된 다른 제한 사항들을 포함하여, ASME Section Ⅷ, Division 1 또는 KS B 6751의 모든 필수 변수들을 반영하여 인정하여야 한다. 압력용기 또는 그 부품의 공칭두께는 부식여유가 포함된 제작두께로 표 7.1의 비고에 나와 있는 제한값을 초과하는 경우, 그 용접부를 표 7.1에 규정된 온도 이상에서 용접 후 열처리를 하여야 한다. 표 7.1의 비고에 제시된 면제사항은 다음 경우에는 허용되지 않는다.
(가) 용접 후 열처리가 충격시험 및 치사성 물질에 규정된 사용요건일 경우
(나) 두께 3 ㎜를 초과하는 페라이트계 재료를 전자빔 용접방법으로 용접할 경우
(다) 임의 두께의 P-No. 6과 7(계열 405 및 계열 410S는 제외)재료를 관성 연속 구동 마찰용접법으로 용접할 경우
(2) 표 7.1의 최소값을 초과하는 유지온도 및/또는 유지시간을 적용해도 된다. 표 7.1에 규정된 온도에서의 유지시간은 연속적일 필요가 없다. 다수 용접 후 열처리 주기의 누적 시간이어도 된다. 용접 후 열처리 온도에 장시간 노출될 경우, 시그마상의 형성 원인이 될 수도 있다.
(3) 다른 두 P-No. 그룹에 속하는 압력 부품을 용접하여 연결할 경우, 표 5.2 또는 표 7.1 중에서 높은 용접 후 열처리 온도가 요구되는 재료에 대한 규정에 따라 용접 후 열처리를 하여야 한다. 비압력 부품을 압력 부품에 용접할 경우, 압력 부품의 용접 후 열처리 온도를 적용하여야 한다. 페라이트계 강 부품을 오스테나이트계 크롬-니켈 스테인리스강 부품 또는 오스테나이트/페라이트 2상계 강과 함께 사용할 경우, 고용화 열처리를 하지 않아야 한다.
(4) 용접 후 열처리 작업은 5. 후열처리 (4)의 요건에 따라 14. 일반적인 후열처리 절차에 제시된 절차들 중 하나로 실시하여야 한다. 다만, 표 7.1의 비고에서 변경하는 경우는 제외한다.
(5) 용접 후 열처리한 압력용기 또는 부품은 용접 보수 후 다시 용접 후 열처리를 하여야 한다.
표 7.1 고합금강의 용접 후 열처리의요건
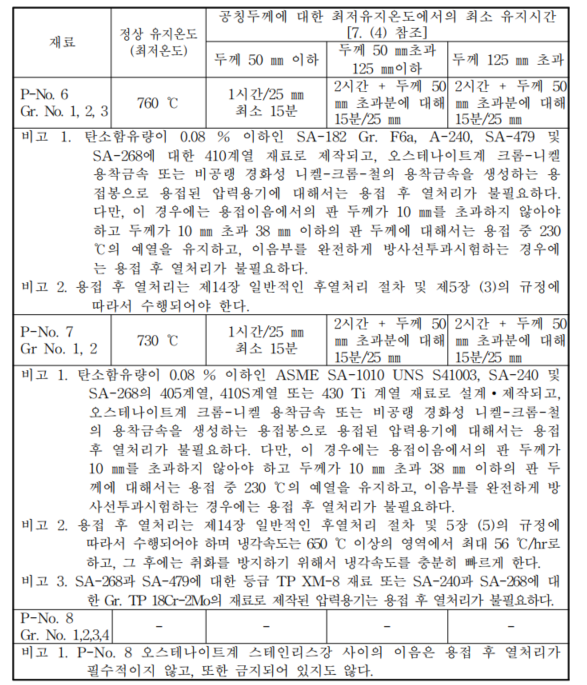
표 7.1 고합금강의 용접 후 열처리 욕건(계속)

8. 페라이트계 압력용기 용접 후 열처리
(1) 페라이트계 압력용기에 적용해야 할 용접절차는 용접 후 열처리 조건 또는 면제 조건 및 아래에 제시된 다른 제한사항들을 포함하여, KS B 6751의 모든 필수 변수들을 반영하여 인정하여야 한다.
(2) 클래드 또는 용착 금속 덧씌움된 압력용기 또는 그 부품에 대하여 표 8.1 페라이트강에 대한 용접 후 열처리에 관한 요건에 따라 용접 후 열처리가 요구되는 두께를 결정하는 경우, 클래드 또는 용착 덧씌움을 포함한 그 재료의 총 두께를 적용하여야 한다.
(3) 표 8.1에 제시된 강으로 설계․ 제작하는 압력용기 또는 그 부품에 대해서는 표 9.1 페라이트강에 대한 용접 후 열처리에 관한 요건에서 요구하는 경우, 용접 후 열처리를 하여야 한다. 다만, 관성 연속 구동 마찰 용접방법으로 재료를 연결하는 경우, 모든 두께에 대해 용접 후 열처리를 하여야 한다.
(4) 표 8.1 페라이트강에 대한 용접 후 열처리에 관한 요건의 요건에 의하여 변경되는 사항을 포함하여 제5장에 따라 용접 후 열처리를 하여야 한다. 어떠한 경우에도 용접 후 열처리 온도는 템퍼링 온도를 초과하지 않아야 한다.
(5) 용접 후 열처리와 템퍼링은 동시에 실시하여도 된다. 5. (4)항 (마)에 따라 결정된 최대 냉각속도를 적용할 필요는 없다.
(6) 재료 표준에서 템퍼링 온도에서 가속 냉각을 요구할 경우, 동일한 최소 냉각속도를 용접 후 열처리에 적용하여야 한다.
(7) 연결부 및 부착부에 대한 모든 용접부에 대해 표 8.1 페라이트강에 대한 용접 후 열처리에 관한 요건에서 요구하는 경우, 경판 또는 동체의 부착 지점에서 재료의 최대 두께를 기준으로 용접 후 열처리를 하여야 한다[위의 (3)에서 (6) 참조].
(8) ASME SA-333 Gr 8, SA-334 Gr 8, SA-353, SA-522, SA-553 및 SA-645의 재료를 용접 후 열처리하는 경우, 이렇게 열처리되는 전체 압력용기 또는 압력용기 구성품은 표 9.1에 정의된 허용온도 범위 이내로 유지되어야 한다.
표 8.1 페라이트강에 대한 용접 후 열처리에 관한 요건

9. 다층(Multipass) 압력용기 용접 후 열처리
(1) 압력 부품은 제5장에서 제9장까지 규정에 따라 용접 후 열처리(요구되는 경우)하여야 하지만, 다층 압력용기 또는 다층 압력용기 부분은 아래 (2)의 요건을 충족시킨다면 용접 후 열처리를 실시할 필요가 없다.
(2) 독성물질용 압력용기, 저온용 압력용기 및 직화식 압력용기가 아닌 경우에는 다층 부분을 다층 부분 또는 중실 벽에 용접 이음부로 연결할 경우, 다층 압력용기 또는 다층 압력용기 부분을 용접 후 열처리할 필요가 없다. 다만, 다음 모든 조건을 충족시켜야 한다.
(가) 제5장 및 제9장에서 참조하고 있는 두께는 한 개 층의 두께이다. 층의 두께가 여러 개일 경우, 가장 두꺼운 층의 두께를 적용한다.
(나) 제5장 및 제9장에 따라 공인검사가 요구되는 중실 부분의 완성된 이음부에는 용접 후 열처리가 요구되지 않는 3 ㎜ 두께의 용접재를 사용한 버터링 층(Buttered layer)을 제공하여야 한다. P-No.1 재료의 중실 부분은 이러한 버터링 층이 있을 필요가 없다. 버터링된 중실 부분의 용접 후 열처리는 다층 부분을 부착시키기 전에 실시하여야 한다. 다층 부분을 용접 후 열처리 하지 않는다면 다층 부분에 부착시킨 후 용접 후 열처리는 요구되지 않는다.
(다) 다층 용접을 실시하고 그 용접층의 두께를 10 ㎜로 제한한다. 페라이트계 강에 대한 규정에 나와 있지 않은 재료를 사용할 경우, 마지막 층은 템퍼 비드 용접방법으로 처리하여야 한다. 다만, 5 %, 8 % 또는 9 % 니켈강의 경우는 제외한다.
10. 저온 압력용기 용접 후 열처리
(1) 5 %, 8 % 또는 9 % 니켈강에 대해서는 8장 페라이트계 압력용기 후열처리 규정을 적용한다.
(2) 5083 알루미늄 합금인 경우에는 비철금속 압력용기 후열처리 규정을 적용한다.
(3) 304계열 스테인리스강의 경우에는 고합금강 후열처리 규정을 적용한다.
11. 배관의 열처리
11.1 용접 및 용접 수리
(1) 용접은 규칙적이고 안쪽 표면에 완전히 침투되도록 하여야 한다
(2) 수리된 용접부위 결함은 금속소재를 제거하여야 한다. 용접 수리부는 검증된 용접절차에 의해 만들어져야 한다.
(3) 수리된 결함부분은 원래 연결부로부터의 면적과 윤곽이 다를 수 있다.
(4) 모든 용접은 자격이 있는 용접사들 또는 용접공이 용접하여야 하며 예열과 열처리는 원래의 용접방법에 따라야 한다.
11.2 예열
(1) 예열과 열처리는 고온과 심한 온도구배의 유해한 영향을 최소화 하기 위해서 실시한다. 예열과 열처리의 필요성은 공학적 설계와 검증된 절차의 입증을 분명하게 하기위해 사용된다. 가(tack)용접, 용접수리, 기밀(Seal)용접, 나사이음 용접 등 모든 종류의 용접에 관해 요구사항과 권장사항이 제공되어있다.
(가) P-No에 따른 재료에 대한 요구 및 권장된 최소 예열온도가 표 11.1에 주어져 있다. 만약 주위온도가 0 ℃ 이하이면, 표 11.1의 권장사항이 요구사항이 된다.
(나) 표 11.1의 두께는 연결부에서 가장 두꺼운 측정 두께이다.
(다) 리스트에 없는 재료에 대한 예열 요구사항은 WPS(Welding Procedure Specification, 용접절차규격서)에 명시되어야 한다.
(라) 예열온도는 WPS에 명시된 온도를 보장하기 위해서 온도 지시 크레용, 열전대 또는 다른 적당한 수단에 의해서 확인되어야 하며, 용접 전과 용접을 하는 동안에 유지되어야 한다.
(마) 열전대는 용접절차와 실행 확인 없이 커패시터 방전 용접을 사용하는 직접적으로 압력을 받는 부분에 붙인다. 열전대를 제거 후에는 수리된 결함의 증거를 위해서 그 영역이 시각적으로 검사되어야한다.
(바) 예열영역은 각 용접의 가장자리를 넘어 적어도 25 ㎜까지 확장한다.
(2) 각기 다른 용접 요구사항을 가진 재료를 한꺼번에 용접할 때에는 표 11.1에 제시된 값 보다 높은 온도를 권장한다.
(3) 용접이 중단된 경우, 냉각속도를 제어해야 하거나 다른 수단을 이용하여 배관에 악영향을 막아야 한다. WPS에 명시된 예열은 용접이 다시 시작되기 전에 적용되어야 한다.
표 11.1 예열온도

출처 : ANSI B31.3 PROCESS PIPING GUIDE R.2 (TABLE330.1.1 PREHEAT TEMPERATURES)
11.3 열처리
(1) 열처리는 용접 시에 고열에 의한 변형 등의 나쁜 영향과 내재된 심한 온도구배를 없애거나 완화시키고, 벤딩(Bending)이나 성형에 의해 생성된 잔류응력을 완화시키기 위해 사용된다. 11.3의 규정에 용접, 벤딩, 성형 조작에 대한 적절한 기본 방법이 있다. 하지만 반드시 모든 사용조건에 적합하지는 않다.
(2) 열처리는 재료 그룹과 11.4의 (2)와 (3)을 제외한 표 11.2의 두께 범위에 따라 하여야 한다.
(3) 공학적 설계는 최종 용접의 적당한 품질을 보장하기 위한 시험과 다른 생산 품질 제어(적어도 이 코드의 요구사항)를 명시하여야 한다.
(4) 벤딩과 성형에 대한 열처리는 다음을 따른다.
(가) 열간 벤딩과 성형 후에, P-No. 3, 4, 5, 6, 10A 모든 두께에 대해 열처리가 요구된다.
(나) 냉간 벤딩과 성형 후에, 모든 두께에 대해 표 11.2에 주어진 온도와 유지시간에 따라 열처리가 요구된다.
➀ 제조자는 P-No. 1부터 6까지는 벤딩이나 성형 후에 계산된 최대 연신율이 해당 사양, 등급, 두께에 대한 최소 연신율의 50%를 초과했을 때. 다만 이 요구사항은 관의 선택과 벤딩 또는 성형의 공정이 가장 심하게 변형된 물질이 적어도 10% 신장이 보증된다는 것을 입증할 수 있는 경우 면제할 수 있다.
② 제조자는 충격시험이 요구되는 모든 재료는 최대 연신율 > 5 % 일 때
③ 공학 설계에서 지정된 때
(5) 용접으로 구성요소가 접합될 때, 사용된 두께는 표 11.2 열처리 요구사항을 적용하고 접합부에서 더 두꺼운 구성요소의 두께를 사용하여야 한다. 다음의 경우는 제외한다.
(가) 지관(갈라지는) 연결부에는 보강으로서 금속의 더해짐, 갈라지는 부속품의 중요한 부분과 보강패드가 붙여지거나 새들 부분은 열처리 요구사항으로 간주되지 않는다. 하지만 용접되는 두께가 최소 재료두께보다 두 배 이상 두꺼울 때 비록 연결부의 구성요소의 두께가 최소 두께보다 얇다고 할지라도 열처리가 요구된다. 용접부 두께는 그림 11.1에 자세히 있고 계산은 다음 식을 이용하여 계산한다.
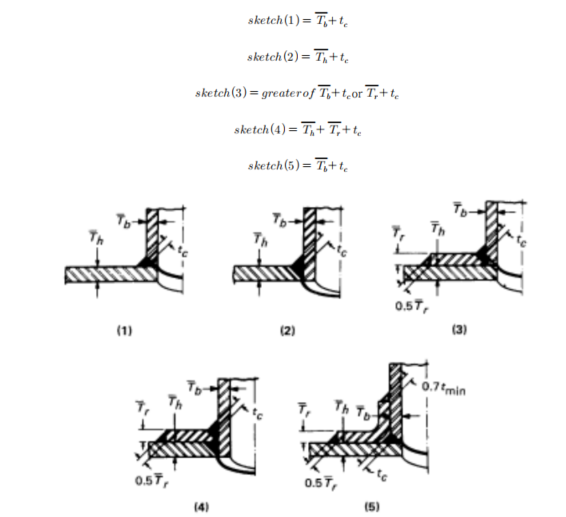
(이 그림은 최소로 허용되는 용접이며, 그림보다 더 크게 할 수 있다.)
그림 11.1 지관 연결부 용접 상세
(나) slip-on에서 필릿 용접과 소켓용접 플랜지, 배관 연결 DN 50(NPS 2)와 더 작은 것, DN 50과 그보다 더 작은 배관의 나사이음의 seal 용접, 외부 비압력 부분의 붙임(러그 또는 다른 배관지지 요소)의 경우, 다음을 제외하고 용접 두께가 최소 재료 두께의 두 배 이상일 경우 연결부의 구성요소의 두께가 최소 두께보다 얇다고 할지라도 열처리가 요구된다.
➀ P-No.1 재료는 모재의 두께와 상관없이 용접 목 두께가 16 ㎜ 이하일 때는 열처리가 요구되지 않는다.
➁ P-No. 3, 4, 5, 10A 재료는 모재의 두께와 상관없이 용접 목 두께가 13 ㎜ 이하 일 때, 모재에 대한 최소 인장강도 490 MPa 이하일 경우 열철리가 요구되지 않는다.
➂ 용접부가 공기 중에서 경화를 하지 않은 페라이트 재료일 경우 요구되지 않는다. 고온에 따른 다른 열팽창, 부식 등으로 용접구조물에 악영향을 주지 않는 경우에는 오스테나이트 용접재료는 페라이트계 재료 용접에 사용될 수 있다.
(6) 가열방법은 요구되는 금속의 가열온도 및 금속의 균일한 온도제어가 되도록 밀폐된 가열로, 국부 가열, 전기 저항, 전기 유도, 화학적 발열반응 등으로 한다. 냉각방법은 요구된 냉각속도를 제공해야 하고, 냉각로, 대기, 국부 가열 또는 단열에 관한 것을 적용함으로써 다른 적당한 수단을 포함해야 한다.
(7) 열처리 온도는 열전대를 이용하여 확인하거나 적당한 방법으로 WPS의 요구사항을 만족하는 것을 확인하여야 한다.
(8) 제품 용접, 열굽힙, 열성형 배관에 대한 경도 시험들은 만족스러운 열처리를 확인하기 위함이다. 경도한계는 가능한 한 용접 가장자리에 가깝게 열영향부와 용접부에 대한 테스트를 적용한다.
(가) 표 11.1에 명시된 경도한계, 각 가열로에서 열처리된 용접부, 열굽힘, 열 성형구성요소의 적어도 10% , 국부적 열처리는 100% 테스트되어야 한다.
(나) 연결부가 이종금속으로 용접되었을 때 경도한계는 표 11.2에 명시된 모재와 용접 재료를 만족시켜야 한다.
11.4 특정한 요구사항
(1) 열처리 경험 또는 조건에 대한 지식으로 보증된 경우, 열처리의 대체방법 또는 11.3의 모재 열처리 규정 예외는 다음 (2)와 11.3에 의해 인용될 수 있다.
(2) 노멀라이징 또는 노멀라이징과 템퍼링 또는 어닐링은 용접 후 또는 굽힘과 성형후에 요구된 열처리 대신에 적용할 수 있다. 용접 영향부의 기계적 성질과 모재가 어떤 처리 후에 만족되거나 대체되어 특정 요구사항을 만족시킨다면 공인검사원에 의해 승인된다.
(3) 11.3에서와 같이, 기본적인 방법이 어떤 경우에 맞게 수정 요구될 수 있다. 이러한 경우에, 설계자는 열처리와 더 얇은 경도한계를 포함한 설계조건에 대하여 더 엄격한 요구사항을 명시할 수 있다. 또는 아무것도 포함하지 않거나, 덜 엄격한 열처리와 경도를 요구할 수도 있다.
(가) 11.3에 명시된 것보다 덜 엄격한 규정일 때. 설계자는 사용자의 만족을 위하여 경험과 비교한 규정, 온도와 영향, 진동과 온도 순환 강도, 스트레스 레벨 유연성, 취성파괴 그리고 다른 적절한 요인 등에 대해서 반드시 적절함을 입증하여야 한다.
(나) 또한, WPS 인정 테스트를 포함하여 적절한 테스트가 실시되어야 한다.
(4) 다른 페라이트계 금속 또는 다른 페라이트 필릿 재료를 사용한 페라이트금속 용접 연결부에 대한 열처리는 표 11.2의 온도범위보다 높은 온도에서 행해져야 한다.
(5) 페라이트계 재료 또는 공학 설계에서 언급된 경우를 제외한 재료에 대해서 페라이트계와 오스테나이트계, 필릿 금속을 포함한 용접연결부의 열처리가 요구된다.
(6) 만약 용접부가 열처리에 앞서 냉각이 허용된다면, 냉각속도가 제어되거나 배관의 나뿐 영향을 막기 위해 다른 수단이 사용되어야 한다.
(7) 열처리되어야 하는 전체 배관 조립체가 가열로 안에 들어갈 수 없을 때, 하나 이상의 열처리가 허용된다. 적어도 300 ㎜ 이상 겹쳐서 유해한 온도구배로부터 보호한다.
(8) 열처리가 국부적으로 적용될 때, 배관에 덮개를 씌우고 용접부 또는 굽힘, 성형부를 포함하여 끝에서 적어도 25 ㎜ 이상을 온도 범위 이상으로 가열해야 한다.
표 11.2 열처리 요구사항
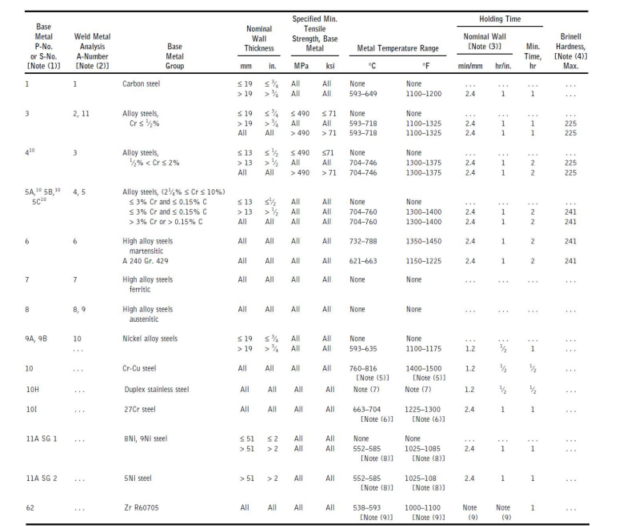
NOTES :
(1) BPV Code, Section IX, QW/QB-422의 P-No 또는 S-No
(2) Section IX, QW-442의 A-No
(3) SI 행렬의 유지시간 단위는 min/㎜. US단위로는 hr/in
(4) 11.4의 (8)을 보아라
(5) 유지기간 후에 가능한 한 빨리 냉각시켜라
(6) 649 ℃까지 냉각속도는 56 ℃(100 ℉)/hr이하여야한다; 그 후에 냉각속도는 취하를 막기에 충분히 빠르다.
(7) 후열처리는 요구되거나 금지되지만 적용되는 어떠한 열처리도 재료의 특성에 따라 요구되어질 수 있다.
(8) 냉각속도 > 167 ℃(300 ℉) ~ 316 ℃(600 ℉)
(9) 용접 후 14일 이내 열처리를 한다. 매 25 ㎜(1 in)이상 마다 유지시간을 1/2 hr를 증가시켜야한다.
냉각속도 278 ℃(500 ℉)이하에서 427 ℃(800 ℉)까지 냉각시킬 때, 매 25 ㎜(1 in) 공칭두께 마다 최대 냉각속도는 278 ℃(500 ℉)이다. 정체 공기중에서는 427℃(800 ℉)부터 냉각시킨다.
12. 냉간성형되는 압력용기 및 부속품의 용접 후 열처리
(1) 냉간성형 결과로 최대 연신율이 압연상태를 기준하여 5 %를 초과하는 경우 다음 조건 중의 어느 하나라도 해당하는 경우에는 냉간성형 이후에 열처리를 하여야 한다.
(가) 재료의 충격시험이 요구될 때
(나) 냉간성형 전에 부품의 두께가 16 ㎜를 초과할 때
(다) 최대 연신율이 5 %를 초과하는 곳 어느 곳이든 압연 두께로부터 냉간성형으로 인한 두께 감소가 10 %를 초과할 때
(라) 성형 중 재료 온도가 120~480 ℃ 의 범위 일 때
(2) 다음 조건들이 주어진 경우, 오스테나이트계 합금강으로 제조한 압력 유지 구성품의 냉간 성형 부위를 급냉 시에 두께의 25 ㎜ 당 20분 또는 10분 중 큰 값에 대해 표 12.1 나와 있는 온도로 가열하여 고용화 어닐링하여야 하며, 후속 급랭시켜야 한다.
(가) 마무리 성형온도가 표 12.1에 나와 있는 최저 열처리 온도 미만인 경우
(나) 설계 금속 온도 및 성형 변형이 표 12.1에 나와 있는 제한값을 초과하는 경우
표 12.1 제작 후 변형률 제한값 및 요구되는 열처리
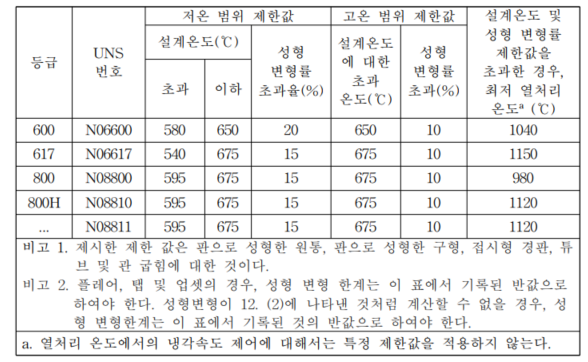
13. 고합금강 및 비철금속 압력용기의 변형에 따른 열처리
(1) 변형으로 인한 제작 후 열처리에 대해 성형에 대한 규정에 추가하여 적용하여야 한다.
(2) 다음의 조건들이 주어진 경우 오스테나이트계 합금강으로 제조된 압력유지 구성품의 냉간성형 면적은 급냉 시에 두께 25 ㎜ 당 20분 또는 10분 중 큰 값에 대해 표 13.1에 주어진 온도로 가열하여 고용화 어닐링하여야 하며, 이어서 급랭시켜야 n한다.
(가) 마무리 성형 온도가 표 13.1에 나와 있는 최저 열처리 온도 미만인 경우
(나) 설계 금속 온도 및 성형 변형이 표 13.1에 나와 있는 제한값을 초과하는 경우
표 13.1 제작 후 변형률 제한값 및 요구되는 열처리

14. 일반적인 용접 후 열처리 절차
14.1 일반사항
(1) 용접 후열처리는 용접절차서와 함께 KS B 6751에서 요구하는 내용을 포함하여 공인검사원의 승인을 받아야 한다.
(2) 용접 후 열처리 작업은 다음 후열처리 절차를 적용하여 사용할 재료에 대한 요건에 따라 실시하여야 한다.
(3) 이 절차에는 표 5.1에 나와 있는 최저 용접 후열처리 온도를 충족 또는 초과시키기 위해 지속 가열대(Soak band)를 금속의 체적으로 정의한다.
(4) 지속 가열대에는 최소한 용접부, 열영향부 및 열처리할 용접부에 인접한 모재 부분을 포함시켜야 한다.
(5) 이 체적의 최소 폭은 용접부의 각 면 또는 끝부분에서 최대 용접부 폭에 1 t 또는 50 ㎜ 중에서 작은 값을 더한 값이다. 이 때 t는 부식여유를 포함한 제작 공칭두께이다.
14.2 후열처리 절차
(1) 가능하면 밀폐된 노 내에서 압력용기 전체를 가열한다.
(2) 압력용기를 노 내에서 두 번 이상 가열할 경우에는 압력용기의 가열 부분을 1.5 m 이상 겹치도록 한다. 노 외부에 있는 부분을 온도구배가 완만하게 하여 재질에 유해하지 영향을 주지 않도록 하여야 한다. 노 외부로 돌출된 압력용기의 단면이 노즐 또는 다른 구조적 불연속부를 가로지르지 않아야 한다.
(3) 압력용기 제작 중에 연결하는 길이방향 이음부 또는 복잡하게 용접된 부분을 용접 후 열처리하기 위하여 압력용기의 동체 부분 및/또는 해당 부위를 가열한다.
(4) 압력용기를 용접 후 열처리 해야 할 필요가 있으나 완성된 압력용기를 전체적으로 용접 후열처리하거나, 위 (2)에 제시된 원주 방향 이음부를 균일하게 가열할 수 있는 적절한 방법으로 국부적으로 가열하여 용접 후 열처리해도 된다. 이렇게 국부적으로 가열할 경우, 전체 원주 둘레로 지속 가열대를 확장하여야 한다. 지속 가열대 외부에 있는 부분은 온도구배가 유해하지 않도록 보호하여야 한다. 새로운 압력용기의 보수 부위를 용접 후 열처리할 때 이 절차를 적용해도 된다.
(5) 압력용기 벽에서의 균일한 온도분포를 제어하고 유지하는 데 도움이 되는 적합한 방법과 적절한 온도 지시 및 기록 장치를 사용하여 내부에서 압력용기를 가열한다.
(6) 이 작업을 실시하기 전에 압력용기를 단열 재료로 완전히 둘러싸거나, 요구 온도에 적합하다면 압력용기에 영구 단열재를 설치해도 된다. 이 절차에서는 내압을 가능하면 낮게 유지하는 것이 바람직하지만, 용접 후 열처리를 하는 동안에 예상되는 최고 금속온도에서 최고 허용사용압력의 50 % 이하이어야 한다.
(7) 전체 가열대를 요구 온도까지 일정하게 하고, 규정시간 동안 유지할 수 있는 방법으로 용접 후 열처리를 필요로 하는 노즐 또는 기타 용접 부착물을 포함하는 원주방향 가열대를 가열한다. 아래 조항에서 변경하는 경우 외에는, 지속 가열대를 전체 압력용기 둘레로 확장하여야 하고, 노즐 또는 용접 부착물을 포함시켜야 한다.
(8) 용접 후 열처리를 요구하는 노즐 또는 부착 용접부에서 떨어진 거리에 따라 원주 방향 지속 가열대 폭을 변화시켜도 되지만, 노즐 또는 부착 용접부 둘레에 요구되는 지속 가열대를 요구 온도로 가열하고 요구시간 동안 유지하여야 한다.
(9) 지속 가열대 폭을 변화시키는 방법에 대한 대안으로, 노즐 또는 부착물에서 떨어져 있는 원주방향 지속 가열대 내의 온도를 변화시켜도 되고, 요구 온도에 도달하지 않아도 되지만, 노즐 또는 부착 용접부 둘레에 요구되는 지속 가열대를 요구 온도로 가열하고, 요구시간 동안 유지하여야 하며, 가열 및 냉각 주기 동안에 온도구배가 유해하지 않아야 한다.
(10) 원주 방향 지속 가열대 외부에 있는 압력용기 부위는 온도구배가 유해하지 않도록 보호하여야 한다. 새로운 압력용기의 보수 부위를 용접 후 열처리할 때 이 절차를 적용해도 된다.
(11) 지속 가열대를 전체 원주 둘레로 확장시키는 적절한 방법으로 관 또는 튜브의 원주 방향 이음부를 가열한다. 지속 가열대 외부에 있는 부위는 온도구배가 유해하지 않도록 보호하여야 한다. 동체 인접부에서는 열적 구속이 증가되며, 따라서 설계자는 노즐 부착부에 유해한 온도구배가 발생되지 않은 상태에서 열처리하거나, 노즐을 포함한 동체 둘레의 원주 방향 지속 가열대 전체를 가열할 수 있도록 적절한 길이를 제공하는 것이 바람직하다.
(12) 이중 곡률의 경판 또는 구형 동체나 경판의 반지름이 큰 부분에 있는 노즐 또는 용접 부착물 둘레의 국부 면적이 요구 온도에 균일하게 도달하여 규정 시간 동안 유지될 수 있도록 그 국부면적을 가열한다. 지속 가열대에 노즐 또는 용접 부착물을 포함시켜야 한다. 지속 가열대에는 모든 방향에서 부착 용접부의 가장자리를 최소한 t 또는 50 ㎜ 중에서 작은 값만큼 확장시키는 범위 또는 원이 포함되어야 한다. 지속 가열대 외부에 있는 압력용기 부위는 온도구배가 유해하지 않도록 보호하여야 한다.
(13) 열적구배(입열속도)의 영향, 중요한 모든 구조적 불연속부(노즐, 부착물, 경판-동체 접속부와 같은) 및 용접 후 열처리할 때 발생할 수도 있는 기계적 하중을 고려하는 다른 조치(문서로 작성된 경험과 평가 결과에 근거한)를 취할 경우, 위 (1)∼ (12)에서 다루지 않은 다른 형상의 국부 면적을 가열할 수 있다. 지속 가열대 외부에 있는 압력용기 부위 또는 구성품은 온도구배를 완만하게 하여 재질에 유해하지 영향을 주지 않도록 하여야 한다.
(14) 용접 후 열처리가 요구될 수도 있는 재료로 설계․ 제작한 압력용기를 용접 후 열처리하기 위한 가열 및 냉각 온도와 속도는 제5장, 제6장, 제7장 및 제8장을 참조한다.
(15) 표5.1, 표 7.1 및 표 8.1, 제6장에 나와 있는 용접 후 열처리 최저 온도는 압력용기 동체 또는 경판의 판재에 대한 최저 온도이어야 한다. 하나 이상의 압력용기 또는 그 부품을 열처리로에 1회 장입하여 용접 후 열처리할 경우, 열처리로 내의 가스온도 측정만으로는 정확하지 않아 압력용기 마다 온도계를 설치하여야 한다.
(16) 다른 두 P-No. 그룹에 속하는 압력 부품을 용접으로 연결할 경우, 보다 높은 용접 후 열처리 온도가 요구되는 재료에 대해 제5장 또는 제7장에서 규정하는 용접 후 열처리를 실시하여야 한다.
(17) 용접 후 열처리가 요구될 경우, 수압시험 전 및 용접 보수 후(제5장 (5)에서 허용하는 경우 제외)에 용접 후 열처리를 하여야 한다. 용접 후 열처리를 하기 전에 누출을 확인하기 위한 예비 수압시험을 할 수 있다.
(18) 표 5.2, 표 5.3, 표 7.1 및 표 8.1에 사용된 공칭두께는 다음에 정의하는 용접 이음부의 두께이다. 열처리로에 장입하여 용접 후 열처리할 압력용기 또는 그 부품에 대한 공칭두께는 이전에 용접 후 열처리하지 않은 압력용기 또는 그 부품의 최대 용접부 두께이다.
(가) 완전 용입 맞대기 용접으로 같은 두께의 부품을 연결하는 용접 이음부의 경우, 공칭두께는 임의의 허용 용접 덧살을 제외한 용접부의 총 깊이이다.
(나) 홈 용접부의 경우, 공칭두께는 홈의 깊이이다.
(다) 필릿 용접부의 경우, 공칭두께는 목 치수이다. 홈 용접과 함께 필릿 용접을 하는 경우, 공칭두께는 홈의 깊이 또는 목 치수 중에서 큰 값이다.
(라) 스터드 용접부의 경우, 공칭두께는 스터드의 지름이어야 한다.
(마) 두께가 다른 부품을 연결하는 용접 이음부의 경우, 공칭두께는 다음과 같아야 한다.
① 판-동체 연결부를 포함한 두 인접 맞대기 용접 부품들 중 얇은 쪽 두께
➁ 그림 14.1에 나와 있는 형식의 중간 경판에 대한 연결부에서 동체 두께 또는 필릿 용접부 두께 중 두꺼운 쪽 두께

그림 14.1 동체에 부착되는 중간 경판
➂ 관판, 평 경판, 덮개, 플랜지(용접부 두께를 적용할 경우, 그림 14.2에 표시된 용접 부품은 제외) 또는 유사 제작품에 대한 연결부에서 동체의 두께
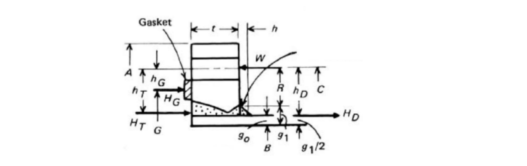
그림 14.2 일체형 플랜지
➃ 그림 14.3 및 그림 14.4에서 노즐 넥, 동체, 경판, 보강 패드 또는 부착물의 필릿 용접부를 가로지르는 용접부 두께 중 두꺼운 쪽 두께
➄ 노즐 넥-플랜지 연결 이음부에서 노즐 넥 두께
➅ 비압력 부품을 압력 부품에 용접할 때 부착 지점에서의 용접부 두께
➆ 튜브-관판 연결부에서 용접부 두께
➇ 여러 층을 적층하는 용접은 적층의 두께
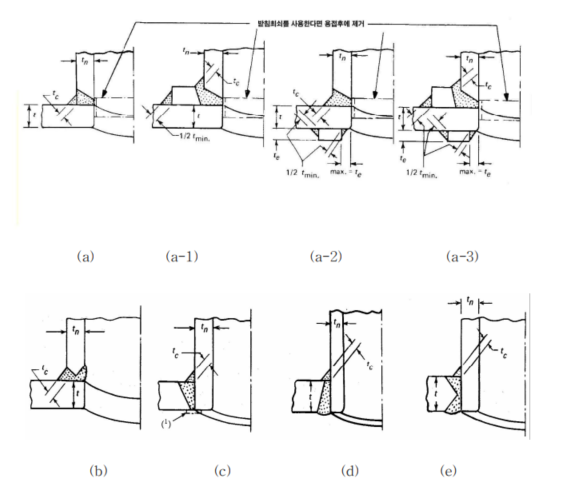

그림 14.3 동체, 경판 등에 용접되는 노즐 및 다른 연결부(계속)

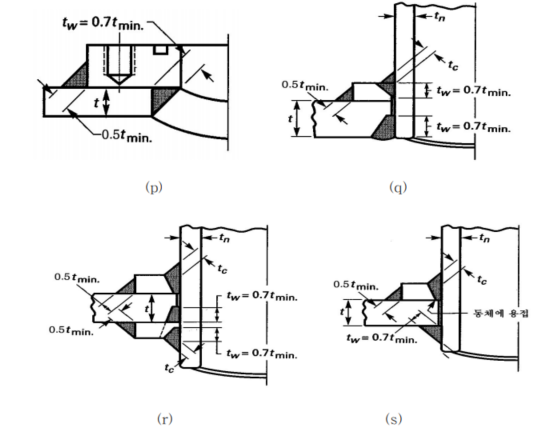
그림 14.3 동체, 경판 등에 용접되는 노즐 및 다른 연결부(계속)
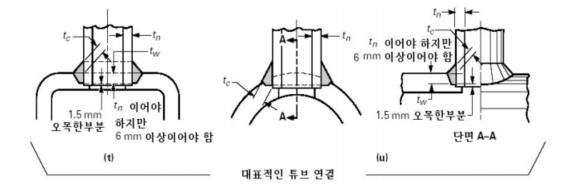
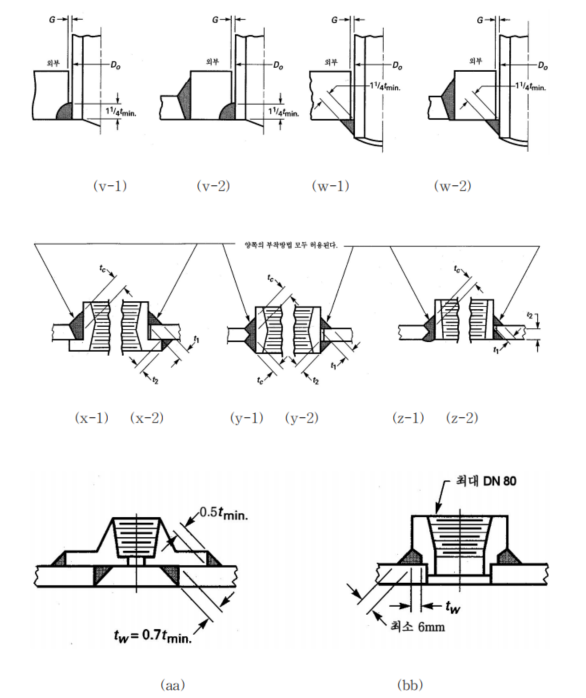
그림 14.3 동체, 경판 등에 용접되는 노즐 및 다른 연결부
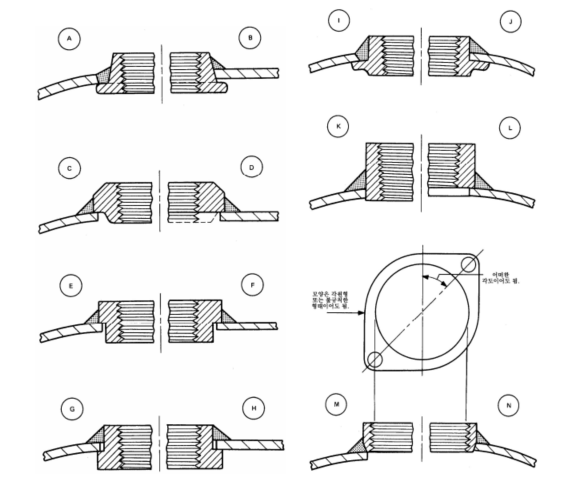
그림 14.4 작은 관이음쇠의 허용 형식
(바) 경판, 동체, 노즐 넥 또는 위에 사용된 다른 부품의 두께는 고려 중인 용접 이음부에서 그 부품의 벽 두께이어야 한다. 판재의 경우, 제조자의 선택에 따라 용접 이음부의 벽 두께를 측정하는 대신 성형하기 전의 재료 시험 보고서 또는 재료의 품질 확인서에 나와 있는 두께를 적용해도 된다.
(사) 보수하는 경우, 공칭두께는 보수 용접부의 깊이이다.
15. 열처리 확인 시험
(1) 제작자가 실시한 열처리 및 후속 열적 처리를 통해 요구되는 성질이 확보되었는지 확인하기 위한 시험을 실시하여야 한다.
(2) 각 압력용기 또는 그 구성품의 재료 및 용접을 대표하는 1개 이상의 시험제를 압력용기 또는 그 구성품과 함께 열처리하여야 한다. 다음 (3), (4)의 요건은 이러한 목적을 달성하기 위한 최소한의 조치로서 이행하여야 한다.
(3) 퀜칭(Quenching)은 다음과 같이 실시한다.
(가) 개별 압력용기 마다 재료의 각 로트(lot)에서 1개 이상의 시험제[아래의 (4) 참조]를 해당 압력용기 또는 그 구성품과 함께 퀜칭하여야 한다.
(나) 한 롯트는 같은 용탕의 재료로써 동시에 퀜칭 또는 노멀라이징(Normalizing)하며, 두께가 공칭두께의 ±20 % 또는 ±13 ㎜ 중 작은 값의 재료로 정의한다.
(다) 시험제는 해당재료 표준에서 요구하는 두께와 동일한 위치에서 인장 시험편 및 충격시험편을 채취하여야 한다.
(라) 용접 금속 시험편은 열처리해야 할 구성품용 판에 대한 해당 재료 표준에서 요구하는 두께와 가능한 동일한 위치에서 채취하여야 한다.
(마) 인장 시험편에서 최소한 1× t 거리에 있어야 한다. 여기에서 t는 그 시험제가 대표하는 재료의 두께이다.
(바) 필요할 경우 적합한 열적 완충재를 임시로 부착하여 이 거리를 확보하여도 된다. 이러한 완충재의 유효성은 시험을 통해 입증하여야 한다.
(사) 열처리할 부품에 시험제를 부착하지 않을 경우, 시험제를 동일한 열처리로에 장입하여 그 시험제가 대표하는 부품과 동일한 조건으로 퀜칭하여야 한다.
(아) 위 (가)에서 (사)에 기술된 위치에서 시험편을 채취할 수 있도록 시험제가 검증되고, 확인되어야 한다.
(4) 템퍼링은 다음과 같이 실시한다.
(가) 부착된 시험제는 템퍼링하는 동안 시험제를 압력용기 또는 그 구성품에 부착시킨 채로 유지하여야 한다. 다만, 퀜칭한 후에 열적 완충재를 제거해도 되는 경우는 제외한다.
(나) 템퍼링 작업 후 그리고 구성품에서 시험제를 제거한 후, 추후 압력용기 또는 그 구성품에 대한 열적 처리와 동일하게 그 시험제를 열적 처리하여야 한다.
(다) 온도의 유지시간은 압력용기 또는 그 구성품에 적용되는 시간 이상이어야 하며
(각 온도에서의 총 유지시간을 1회의 가열 주기에 적용해도 되는 경우는 제외
한다.), 냉각속도도 이보다 빠르지 않아야 한다.
(라) 분리된 시험제는 위 (3)의 (사) 및 (아)에 기술된 바와 같이 분리하여 퀜칭한 시험제는 그 시험제가 대표하는 압력용기 또는 구성품과 유사하게 그리고 동시에 템퍼링 하여야 한다. 그 시험제에 대한 후속 열적 처리 조건은 위 (가)에서 (다)에 기술된 바와 같다.
(5) 시험횟수는 하나의 인장 시험편 및 하나의 충격시험편을 열처리한 각 압력용기 또는 그 구성품 재료의 각 로트를 대표하는 시험제에서 채취하여야 한다. 한 로트는 동시에 퀜칭한 동일한 용탕의 재료로써 두께가 공칭두께의 ±20 % 또는 ±13 ㎜ 중 작은 값의 재료로 정의한다.
(가) 용접부가 포함되지 않은 시험제는 해당 재료 표준의 모든 인장 요건 및 페라이트계 강 압력용기에 대한 충격 요건을 충족시켜야 한다.
(나) 용접 금속이 포함되는 시험제는 용접부를 가로질러 시험하여야 하며, 해당 재료 표준의 최대 인장강도 요건을 충족시켜야 한다. 또한 용접 금속에 노치를 가공한 시료를 사용하여 최소 충격요건을 충족시켜야 한다. 인장 시험편의 형상과 치수는 그림 12.1 단면감소 인장 시험편 - 선삭 봉형 시험편(KS B 6751의 그림 29.2.1 d))를 준수하여야 한다.
(6) 검사원은 모든 용접 후 열처리의 정확한 실시 및 열처리 온도가 해당요건을 준수하고 있는지 확인하고, 명판에 표시되어 있음을 확인하여야 한다.
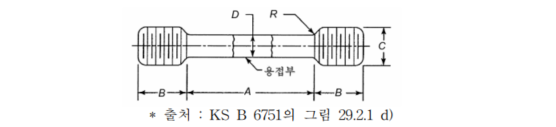
그림 15.1 단면감소 인장 시험편 - 선삭 봉형 시험편
표 15.1 시험편의 치수
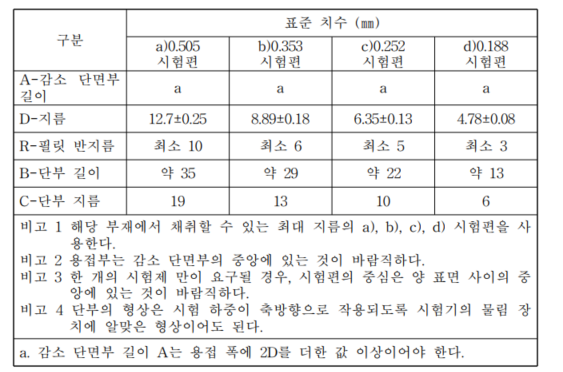
(가) 항복강도 및 연신율은 이 시험 요건이 아니다. 샤르피 충격시험은 KS B 6750 5.11.2의 요건을 따라야 한다.
16. 온도 측정 및 기록
(1) 온도는 원칙적으로 피가열부를 대상으로 해서 열전대에 의해 자동적으로 측정하고, 그래프와 기타 방법으로 기록하여야 한다.
(2) 노내 온도에서 가열부의 각 부의 온도를 추정할 수 있는 경우에는 노 내의 낮은 온도로 대신하여도 상관없다.
(3) 열전대는 최대 측정범위의 50 % 전후가 권장된다.
(4) 열전대는 공인검사원의 승인을 받아 가열원의 반대 측에 여러 개를 설치한다.
(5) 다음 항목을 반드시 기록하고 공인검사원의 승인을 받아야 한다.
(가) 노 또는 가열장치의 종류 및 형식
(나) 유지온도 및 유지시간
(다) 가열속도 및 냉각속도
(라) 기록지에 측정위치, 범위 및 단위 시간당 속도
(마) 입회자의 확인 및 서명
(바) 기타 필요한 사항
[첨부자료] 압력용기 용접 후 열처리에 관한 기술지침(M-184-2015)
'산업안전' 카테고리의 다른 글
설비배치 계획 및 변경시의 리스크 평가지침(X-60-2013) (0) | 2022.03.17 |
---|---|
리스크 분석 방법에 관한 지침(X-19-2012) (0) | 2022.03.09 |
고장형태와 영향분석(FMEA)기법에 관한 지침(X-6-2012) (0) | 2022.03.08 |
축전지 취급에 관한 기술지침(E-10-2013) (0) | 2022.03.07 |
가스 폭발위험장소의 전기설비 검사 및 정비에 관한 기술지침(E-101-2014) (0) | 2022.03.07 |