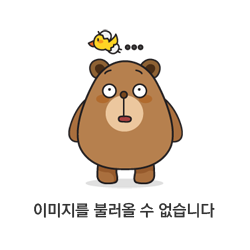
o 관련 규격 및 자료
- BP, Hazards of Oil Refining Distillation Units, ICheme, 2008
- BP, Safe Furnace and Boiler Firing, ICheme, 2005
- BP, Hazardous Substances in Refineries, ICheme, 2005
- BP, Hazards of Water, ICheme, 2004
- BP, Hazards of Nitrogen and Catalyst Handling, ICheme, 2006
- BP, Hazards of Steam, ICheme, 2004
- Henry Z Kister, Distillation Operation, McGraw-Hill, 1990
- Norman P.Lieberman, Process Design For Reliable Operations 2nd Ed, Gulf, 1988
- UOP, Engineering Design Seminar Training Material, 2006
- Penn State College of Earth and Mineral Sciences e-education institute homepage
- ANSI/API, RP 571 Damage Mechanisms Affecting Fixed Equipment in the Refining Industry 3rd Edition, 2020
- API RP 578 Material Verification Program (MVP) for New Existing Alloy Piping Systems 3rd Edition, 2018
- API STD 610 Centrifugal Pumps for Petroleum, Petrochemical, Natural Gas Industries 12th
- API STD 617 Axial and Centrifugal Compressors and Expander-Compressors, 2016
- ANSI/API 618 Reciporcating Compressors for Petroleum, Chemical, and Gas Industry Services 5th, 2016
- HSE, CRR 205/1999 Selection Criteria for the Remote Isolation of Hazardous Inventories
- Clifford Jones, Hydrocarbon Process Safety 2nd Edition, Whittles Publishing, 2014
- 안전보건공단, 석유화학공정 심사기술편람 상압원유 정제공정
- 삼성화재, 에너지 화학산업 선진 방재기술기준, 2006
정유시설의 안전 운영에 관한 일반적인 위험관리에 대한 기술지침(P-174-2021)
1. 목적
2. 적용범위
3. 정의
4. 공정 개요
5. 취급 물질 위험성 및 대책
6. 공정 가동시작 및 가동정지 안전대책
7. 정상 운전 안전대책
8. 정기보수 위험성
9. 공정 설비 손상 및 고장 대책
1. 목적
이 지침은 대용량의 원유(Crude oil)를 가열 및 증류하여 석유제품을 제조, 취급하는 시설로 화재, 폭발 및 위험물질 누출 위험성을 가지고 있는 상압 및 감압증류공정 중심인 정유공정(Refinery process)에 대한 것으로서 공정 설계, 운전 및 설비관리시 발생 가능한 위험 요인(Hazard)을 이해하여 정유공정 및 석유화학공정에서 발생 가능한 사고를 예방하고, 피해를 최소화하는데 그 목적이 있다.
2. 적용범위
이 지침은 정유공정에 대한 위험성을 제어하는 것으로 작성되었으며, 정유공정과 유사한 설비를 보유하고 대량의 인화성 물질을 제조, 취급하는 석유화학공정(Petrochemical process)에서도 전체적으로 적용할 수 있다. 단, 본 지침은 고온 및 고압의 중질유 수첨분해공정 및 유동층촉매분해공정, 대규모 인화성 물질 저장탱크 등의 특정 공정 및 저장시설은 포함하지 않았다.
3. 정의
(1) 이 지침에서 사용되는 용어의 정의는 다음과 같다.
(가) “상압증류공정(Crude distillation unit, CDU)” 이라 함은 상압 조건 하에서 350 ∼370℃ 수준으로 가열한 원유를 증류탑에 주입하여 각 성분별 탄화수소 화합물의 비등점 차이를 이용하여 LPG, 납사, 등유, 경유 및 상압잔사유 등의 반제품을 분리하는 공정을 말한다.
(나) “감압증류공정(Vacuum distillation unit, VDU)”이라 함은 상압증류공정으로부터 추가 분리가 어려운 상압잔사유(압력 조건에 따라 달라지나 약 400℃ 수준에서 탄화수소의 열분해가 심화될 수 있다.)를 원료로 하여 대기압보다 낮은 압력에서 상압잔사유 내 존재하는 탄화수소 화합물의 비등점을 낮추어 감압경유(Vacuum gas oil, VGO)를 추가 분리하여 후단 공정의 중간 원료 또는 아스팔트 등을 제조하고 중간 제품을 분리하는 공정을 말한다. 감압경유는 중질유분해공정이나 윤활유 제조공정의 원료로 사용될 수 있으며, 감압경유 분리 이후 남은 감압잔사유는 아스팔트 원료나 고유황 중유로 활용될 수 있다.
(다) “휘발유제조시설(Platforming unit, PF)”이라 함은 촉매독 등을 제거하는 수첨탈황공정(Naphtha hydrotreating unit, NHT), 수소와 함께 탈황된 납사를 백금촉매와 반응시켜 개질유(Refrormate)를 생산하는 접촉개질공정(Reformer), 개질유에서 벤젠을 제거하는 벤젠저감공정(Benzene recovery plant, BRP) 등으로 구성되는 공정을 말한다.
(라) “탈황공정(Hydrodesulfurization)”이라 함은 탈황 촉매가 충진된 고온⋅고압의 반응기에서 수소를 첨가하여 정제 제품 중의 황분을 제거하는 것을 주요 목적으로 하는 공정을 말한다.
(마) “탈염기(Desalter)”라 함은 원유 자체 또는 이송 중 포함된 선박 평형수(Ballast water)로 인해 원유에 포함된 염분을 제거하는 설비로 전기나 화학적 방법으로 염분, 회분, 수분 등을 제거한 후 다시 승온 및 예열하기 위해서 열교환기로 이송하는 설비를 말한다.
(바) “브라인 워터(Brine water)”라 함은 탈염기에서 상부로 유분이, 하부로는 물이 분리되는데, 일반적으로 탈염기의 하부로 유출되는 소금, 고형물질(철, 진흙 등)을 함유한 물을 말한다.
(사) “가열로(Fired heater)”라 함은 탄화수소 원료를 적정 온도로 가열하여 증류탑이나 반응기로 이송시키는 설비로, CDU에서는 350℃ 이상, VDU에서는 400℃이상 가열하는 설비를 말한다.
(아) “파울링(Fouling)”이라 함은 배관 내부 등의 표면적에 발생한 이물질과 퇴적물의 축적을 말한다.
(자) “스위트닝(Sweetening)”이라 함은 일반적으로 메록스(Mercaptan oxidation, Merox) 공정으로 불리우며, 탄화수소 내 머켑탄(Mercaptan) 형태로 존재하는 유황 성분을 제거 또는 전환시키는 공정을 말한다.
(차) “데드렉(Dead leg)”이라 함은 배관의 가지 부분, 탱크에 연결된 배관 등의 연결부분에서 유체가 정체되는 구간을 말한다.
(2) 기타 이 지침에서 사용하는 용어의 정의는 이 지침에 특별한 규정이 있는 경우를 제외하고는 산업안전보건법, 같은 법 시행령, 같은 법 시행규칙 및 산업안전보건기준에 관한 규칙에서 정의하는 바에 따른다.
4. 공정 개요
4.1 설계 및 운전 개요
관련 기술기준은 공정안전 설계, 운전, 설비관리 측면으로 참조할 수 있도록 기술하였으며, 관리절차는 기본적으로 공정안전보고서의 제출⋅심사⋅확인 및 이행상태평가 등에 관한 규정에 따라 공정안전관리(Process safety management, PSM)를 적용하므로 본 기술지침에서는 제외한다.
(1) 제조 시설
(가) <그림 1>과 같이 원유는 원유 운반선에서 이송 배관과 저장 탱크를 거쳐 정유공정으로 유입되어 상압증류공정(Crude distillation unit, CDU)과 감압증류공정(Vacuum distillation unit, VDU)을 거쳐 다양한 비등점을 가진 물질들을 분리한다.
(나) 다양한 종류의 원유는 각 비율에 따라 가스, 휘발유, 경유, 등유, 항공유, 윤활유, 아스팔트 및 납사 등의 다양한 제품을 비율에 따라 생산한다. 원유는 비등점의 차이로 최초 증류가 일어나는 상압증류탑에 이송되기 전에 약 350∼370℃로 가열된다.
(다) 상압증류탑으로부터 생산된 상압잔사유는 필요한 성상에 따라 감압증류탑에 유입되기 전에 400 ~ 434℃ 까지 조금 더 가열된다.
(라) CDU/VDU에서 분리된 탄화수소 반제품들은 후단 휘발유제조시설, 탈황공정 및 중질유분해공정 등에서 추가 처리되어 최종 제품을 생산한다. 관련하여 전체적인 공정은 <그림 2> 와 같다.
(마) 제조시설 관련 기술기준은 미국정유협회(American petroleum institute, API), 미국기계기술자협회(American society of mechanical engieers, ASME), 미국 국가표준협회(American national standard institute, ANSI), 미국시험재료학회
(American society of testing material, ASTM), 미국소방협회(National fire protection association, NFPA)에서 규정하는 기준들에 따라 설계, 제작 및 건설된다. 또한, KOSHA Guide D-15 화학설비의 재질선정에 관한 기술지침, D-5 화학공정의 시스템 디자인 크라이테리어에 관한 기술지침, D-52 배관 계통의 공정 설계에 관한 기술지침, D-18 안전밸브 등의 배출용량 산정 및 설치 등에 관한 기술지침, D-37 화학설비 등의 공정설계에 관한 기술지침, D-24 화학설비의 안전설계 일반기준에 관한 기술지침을 적용할 수 있다.
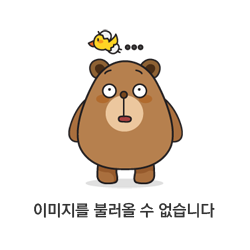
<그림1> 정유공정 흐름도
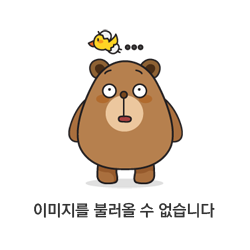
<그림 2> CDU/VDU 개요도
(2) 저장 시설
(가) 해당 원재료, 중간재료 및 최종 생산품을 각 공정에 따라 저장하는 것으로 KOSHA Guide D-35 상압저장탱크의 설계에 관한 기술지침, API PUBL 2510A Fire Protection Consideration for the Design and Operation of Liquefied Petroleum Gas(LPG) Storage Facilities에 따라 안전 설계를 적용한다.
(나) 저장탱크 관련 작업은 KOSHA Guide P-165 인화성 물질 상압저장탱크의 안전작업에 관한 기술지침, KOSHA Guide D-57 가스상 급성 독성물질의 하역 및 출하시 안전기준에 관한 기술지침을 참조하여 수행한다.
(3) 유틸리티
(가) 운전에 필요한 스팀, 전기, 용수, 압축공기, 냉각수, 질소 및 연료유를 제조, 취급, 저장하여 정유 공정에 공급하는 설비이다.
(나) 전 공정을 대상으로 각 공정 운전에 필요한 유틸리티를 안정적이고, 경제적으로 생산하여 생산 공정에 지속적으로 공급하는 것을 목적으로 한다.
(다) 특히, 압축공기, 질소 등에 대해서는 KOSHA Guide P-121 공기분리설비의 안전설계 및 운전에 관한 기술지침, KOSHA Guide P-150 유해위험공간의 안전에 관한 기술지침을 참조하여 안전관리에 적용한다.
(4) 환경설비
(가) 공정에서 배출되는 폐수, 폐가스, 폐기물의 처리를 위한 설비로 폐수처리장, 폐기물 저장소, 대기 배출시설 등이다.
(나) 특히, 폐가스 처리를 위한 소각을 위해서는 KOSHA Guide P-66 연소소각법에 의한 휘발성유기화학물(VOC) 처리설비의 기술지침을 준용하고, 폐수처리장은 KOSHA Guide P-148 화학공장 폐수 집수조의 안전조치에 관한 기술지침을 적용할 수 있다.
(5) 공정 배출 시설
(가) 공정 배출 시설은 API STD 521 Pressure-relieving and Depressuring Systems, API STD 537 Flare Details for Petroleum, Petrochemical, and Natural Gas Industries를 기준으로 KOSHA Guide D-59 플래어시스템의 설계 설치 및 운전에 관한 기술지침을 적용한다.
(나) 공정 배출시설은 공정 안전 측면으로만 한정하며, 이외 상시 배출은 환경 설비의 배출 시설로 적용해야 한다.
(6) 능동⋅수동 소방시설(Active⋅Passive fire protection system)
(가) 능동 소방시설은 API RP 2001 Fire Protection in Refineries를 기준으로 KOSHA Guide P-115 정유 및 석유화학공장의 소방설비에 관한 기술지침, KOSHA Guide P-167 정유 및 석유화학 산업의 고정식 물분무설비의 설계 등에 관한 기술지침, CCPS Guidelines for Fire Protection in Chemical, Petrochemical and Hydrocarbon Processing Facilities 에 따라 적용한다.
(나) 수동 소방시설로서는 추가로 내화처리 관련의 API PUBL 2218 Fireproofing practices in petroleum and petrochemical processing plants, KOSHA Guide D-45 내화구조에 관한 기술지침을 적용한다.
(7) 공정지역 내 건축물
(가) 공정 지역 내 건축물은 API RP 752 Management of Hazards Associated with Location of Process Plant Permant Buildings, API RP 753 Management of Hazards Associated with Location of Process Plant Portable Buildings, KOSHA Guide D-32 제어실의 위치선정 및 설계에 관한 기술지침을 적용한다.
(나) 사업장 내 고정식 및 이동식 건축물 설치시 공정 화재⋅폭발 및 독성 가스 누출에 대한 위험성을 고려하여 위치 선정 및 설계를 해야 한다.
4.2 위험성 개요
(1) 정유공정에서는 인화성 물질이 자연발화점 이상인 360∼434℃로 제조, 취급되면서 화재, 폭발 위험성이 있다.
(2) 이때 원유에 포함된 황의 함유량에 따라 사우어(Sour)/스위트(Sweet)로 구분하고, 황에 의한 산성으로 설비 재질의 부식은 가속화될 수 있다. 정유공정은 프로젝트 단계부터 특정한 원유 혼합물을 기준으로 설계되며 일반적으로 대부분의 공정은 넓은 범위의 다양한 원유를 처리 및 운전할 수 있도록 건설해야 된다.
(3) 황화수소(H2S)와 염화염(Chloride salt)은 가장 지속적인 위험성을 정유공정에 줄 수 있으므로 공정은 처리되는 원유에 의한 부식과 침식 등을 견딜 수 있는 재질로 설계해야 한다.
(4) 원유의 염화물(NaCl, MgCl2, CaCl2) 중 MgCl2, CaCl2 등은 상압증류공정 운전온도에서 가수분해되어 염화수소를 형성하여 상압증류탑의 상부 시스템에서 부식을 심화시키므로 원유에 포함된 염화물을 제거하기 위해서는 성능이 우수한 탈염기의 설계와 운전이 중요하다. 이에 따른 폐수처리장은 탈염기로부터 배출되는 브라인 워터(Brine water)를 처리할 수 있어야 한다.
(5) 다음과 같은 항목에서는 KOSHA Guide D-15 화학설비의 재질선정에 관한 기술지침, API RP 571 Damage Mechanisms Affecting Fixed Equipment in the Refining Industry를 참조하여 재질 선정과 설비보존 주기를 결정해야 한다.
(가) 정상 운전 중 재질 부식, 배관 연결 부위나 설비 보수 중 누출로 인화성 물질의 화재, 폭발 또는 독성가스(H2S) 확산에 의한 인체 상해가 가능하다.
(나) 인화성 물질의 누출과 반대로 감압증류공정의 잠재 위험성은 설비 내로 외부 공기의 유입이다. 소량의 공기 유입으로도 감압증류공정 내 인화성 물질이 지배적인 환경에서 점화가 가능하다. 때때로 ‘냉염(Cool flames)’이라 불리우는 국부적이고 느린 속도로 연소하는 고열은 탑조류 내부 시스템에 기계적 손상을 줄 수 있다. 또한, 대량의 공기 유입으로 감압증류공정 내부에서 인화성 물질과 혼합되어 사우어 가스(Sour gas)를 점화시킬 수 있다.
(다) 공정에서 액체 및 기체 연료의 연소로 에너지를 공급하는 가열로가 다수 있다.
가열로는 연료의 연소열을 이용해 공정 원료를 직접 가열하는 방식이므로, 공정 원료를 담고 있는 가열로 내부 튜브 및 누출시 가열로 내에서 점화 및 폭발을 일으킬 수 있다.
(라) 공정으로 도입되는 원유는 수분을 일부 함유하고 있다. 만일 저장 탱크 운전이 적정하게 제어되지 않거나, 탈염기가 제거해야 할 비말동반된 수분에 의해 공정 배관 내 슬러그(Slug)가 유입될 수 있다. 배관 내 형성된 슬러그는 탑조류 내부에 손상을 주고 공정 설비에 과압을 줄 수 있다.
(마) 원유는 다양한 유기물질과 무기물질을 함유하고 있고, 원유 내, 설비 재질 또는 건설된 물질들과 반응하여 부식 물질을 만들어 낼 수 있다.
(바) 공정 가동 정지 중에 증류탑 내에서 자연발화로 인한 화재가 발생할 수 있다.
특히 내부 탑조물 충진물과도 반응할 수 있다.
(사) 가동시 비정상 운전은 공정 상태를 악화시킬 수 있으며, 특히 기체 배관에 액체가 유입되는 이상 운전과 드라이런(Dry run) 펌프 현상 등은 공정안전 위험성을 높일 수 있다.
1) 오버헤드 기상 배관으로 슬러그가 유입될 경우에는 오버헤드 배관 자체와 배관 지지대 등에 과부하가 발생하여 물리적 손상을 줄 수 있다.
2) 기상 유체 시스템의 압력 밸브 상부에 액상 슬러그가 축적되면서 기체가 취급되는 시스템에 액체가 유입되어 관련 배관과 지지대, 플레어 넉아웃 드럼(Flare knock out drum)의 과충전 등으로 기계적 과부하로 인한 손상을 줄 수 있다.
4.3 주요 사고 발생시기
(1) 일반적으로 공정 전(全) 기간에 발생할 수 있지만, 가장 취약한 시기는 가동 시작(Start-up)과 가동 중단(Shut down)이다.
(2) 가동 시작과 가동 중단을 위한 운전 기간은 일반적인 정유공장에서 3년∼4년에 한달 정도의 시간비율로 약 3% 미만이지만, 사고 발생 비율은 전체 사고 건수 중 약20%로 가장 많은 사고가 발생하는 시간대이다. 이외 정기보수 기간이 두 번째로 취약하고, 세 번째가 정상운전 순이다.(미국 BP 사업장 사고 통계 기준 참조)
5. 취급 물질 위험성 및 대책
주 제조 공정 외에 부산물 또는 추가 물질로 제조⋅취급⋅저장되는 물질에 대한 위험성도 전체 공정안전 위험성에 영향을 줄 수 있으므로 포함하여 기술한다.
5.1 탄화수소 물질(Hydrocarbon)
(1) 원유(Crude oil)
원유는 메탄부터 아스팔트까지 넓은 범위의 다양한 탄화수소들로 구성되어 있다. 원유가 성상에 따라 상온, 상압에서 인화점 이상인 인화성(Flammable)이 있거나, 충분한 점화 에너지로 점화되도록 인화점 이상으로 온도를 올리는 가연성(Combustible)을 가지고 있다.
(2) 경질유분(Light hydrocarbon)
(가) 경질유분은 일반적으로 <표 1>과 같이 C1부터 C6까지로 상온에서 누출되거나, 중질유분이 인화점 이상에서 기상 상태로 누출시 점화가 가능하다.
<표 1> 원유 관련 물질 성상
물질 | 공기 중 농도 (vol%) | 자연발화점(℃) | 인화점(℃) | |
LEL | UFL | |||
원유 | 0.6 | 15.0 | 400 이상 | -7 ~32 |
메탄 | 5.0 | 15.0 | 650 | -153 |
에탄 | 2.1 | 9.5 | 472 | - |
프로판 | 2.1 | 9.5 | 450 | -105 |
부탄 | 1.9 | 8.5 | 287 | -60 |
가솔린 | 1.0 | 7.5 | 223 ~338 | -42 ~ -32 |
납사 | 1.1 | 7.5 | 223 ~ 338 | -42 ~ -32 |
등유 | 1.2 | 6.0 | 225 | 40 ~50 |
황화수소 | 4.3 | 46.0 | 260 | -82.4 |
경유(가스 오일) | 0.5 | 5.0 | 338 | 116 ~120 |
상압 잔사유 | 1.0 | 6.0 | 350 이상 | 100 이상 |
중유 (Bunker Oil) | - | - | 407 이상 | 100 이상 |
(나) 경질유분은 누출시 증기운을 형성하여 공정 내 점화원인 가열로, 화기작업, 차량 및 비방폭 설비가 위치한 지역까지 흘러갈 수 있다. 이것을 통해 증기운은 해당 지역 및 외부까지 화재, 폭발을 일으킬 수 있다.
(다) 또한, 누출시 바로 점화가 되면 배관이나 공정 설비 등에 분출 화재(Jet fire)로 화염이 설비에 바로 열적 손상을 줄 수 있는 화염 충돌(Flame impingement; 불꽃이 설비에 직접 닿는 현상)이 발생할 수 있다.
(라) 일부 중질유분들은 고온에서 열분해가 발생한 경질유분와 황화수소로 구성되어 저장탱크 등에서 화재, 폭발을 발생할 수 있다.
(3) 중질유분(Heavier hydrocarbons)
(가) 중질유분은 자연발화온도(Auto-ignition temperature, AIT) 이상으로 운전될 경우 <표 1>과 같이 중질유분은 일반적으로 낮은 자연발화온도를 가지고 있어 외부 누출시 점화되어 액면 화재(Pool fire)가 발생할 수 있다.
(나) 공정에서 누출되는 중질유분이 자연발화온도 이상으로 운전되는 설비에 접촉시에도 점화되어 화재⋅폭발이 가능하다.
(다) 액면 화재는 분출 화재(Jet fire)보다 강도는 낮지만, 넓은 범위에 복사열 영향을 줄 수 있다.
5.2 누출 가능한 무기물질
(1) 황(Sulfur)
(가) 원유 내 가장 전형적인 무기물질은 황이며, 황화수소(H2S) 형태로 정유 공정에서 기체 내에 포함된다. 황화수소의 8시간 시간가중평균허용기준(Threshold limit value-Time weighted average, TLV-TWA)은 10 ppm, 단시간노출허용기준(Shot time expousre limit, STEL)은 15 ppm이며, 1000 ppm 초과시 바로 사망할 수 있다.
(나) 황화수소는 달걀썩은 냄새가 나고, 농도가 높아지면 흡입자의 후각을 급속도로 마비시킬 수 있어, 황화수소가 누출 후에도 흡입자가 황화수소가 없다는 착각을 일으킬 만큼 감각이 마비되어 농도가 높은 지역에서 바로 쓰러져 상해가 발생할 수 있다.
(다) 티올(Thiols)은 유기 황물질로 머켑탄(Mercaptan)의 가장 일반적인 형태로 존재하며, 낮은 농도에서도 고 독성(High toxic)으로 악취가 발생하여, LPG 등의 제품에 부취제인 에틸 머켑탄(Ethyl mercaptan) 등으로 사용하기도 한다. 고온에서는 티올은 열분해로 황화수소를 생성할 수 있다.
(2) 나프텐산(Naphtenic acid)
(가) 나프텐산은 CnH2n-1COOH를 형성하는 싸이클릭 카르복실산의 한 종류로 특정 원유에 함유될 수 있다.
(나) 일반적으로 원유 내 농도로는 작업 중 노출 위험성은 높지 않지만, 공정 시설의 부식의 원인으로 작용할 수 있으므로 KOSHA Guide D-15 화학설비의 재질선정에 관한 기술지침, API RP 571 Damage Mechanisms Affecting Fixed Equipment in the Refining Industry를 참조하여 재질 선정 및 설비보존 주기를 결정해야 한다.
(3) 유기염화물
(가) 유기염화물은 원유에 자연적으로 존재하며, 유정과 정유공장에서 첨가제로 투입될 수 있으며, 직접적인 산업보건 측면 노출 위험성은 없지만, 염화수소의 원재료로 사용되어 후단 공정에서 부식을 일으킬 수 있다.
(나) 공정 중에서는 아민(Amine)으로 중화시키므로, 운전 중 증류탑의 오버헤드 액상 배관에서 유기염화물 함유량에 따라 중화를 위한 첨가제 농도를 모니터링하기 위해 상시 검사를 해야 한다.
(4) 염(NaCl, MgCl2, CaCl2 등)
(가) 지중(Underground)에 상시 존재하는 물질로 원유에 포함된 수분에 정상적으로 존재하는 염과 다른 용수로부터 용해된 무기질 요소들을 말한다.
(나) 공정상 부식 위험성과 연관이 되어 있으며, 특히 원유 내 수분은 항상 독성을 가지고 있음을 주의해야 한다. (예. 황화수소 흡입, 섭취, 피부와 눈에 접촉 등)
(5) 수은
(가) 수은은 단일 물질로, 원유 내 유기⋅무기물질에 함유되어 다양한 형태로 존재할 수 있다.
(나) 수은은 농도에 따라 후단 공정에 촉매독으로 작용할 수 있고, 제품 품질을 저하시킬 수도 있다.
(다) 또한 수은은 경질유가 제조되는 후단 공정의 재질에 손상을 줄 수 있고, 폐수성상에서 법규를 충족시키는데도 문제가 될 수 있으므로 탈염기 등으로 최대한 제거해야 한다.
(6) 방사능 물질 (Normally occurring radioactive materials, NORM)
(가) NORM은 공정 설비 내벽에 쌓이는 퇴적물 중 라듐(Ra)과 플로늄(Po) 방사능 동위원소를 포함한 원유 내 퇴적물 내에서 방사성 감쇠를 통해 발생되는 부산물을 말한다.
(나) 일반적으로 이것은 원유나 천연가스 체굴시부터 발생하여 정유공정까지 이어진다. 일반적으로 정유 공정의 NORM은 방사능이 증가하여도 운전 중에는 문제가 없지만, 공정 설비 보수나 검사를 위해 해당 설비를 개방시 내부의 먼지 등에 포함되어 밀폐공간 작업 등에 출입하는 작업자에게 흡입과 섭취로 산업보건측면 유해요인을 발생시킬 수 있다. 따라서 KOSHA Guide H-80 밀폐공간 작업 프로그램 수립 및 시행에 관한 기술지침에 따른 안전조치를 적용한다.
(7) 고형물
(가) 모래나 배관 내 부식 등으로 발생하는 스케일(Scale) 등의 고형물들이 공정 내부에서 퇴적될 수 있다. 대부분의 고형물은 침전물로 존재하여 탈염기에서 제거된다. 그러나 만일 탈염기 후단 공정에서 침전될 수 있다면 설비 관리나 검사를 위해 출입하는 작업자들에게 산업보건 측면의 위험요인이 될 수 있다.
(나) 따라서, 내부 침전물 제거시나 해당 밀폐공간 출입시 반드시 적정 호흡보호구를 착용하고, 원유 도입시 원유 운반선이나 원유 탱크 바닥 퇴적물 및 수분(Bottom sediment and water, BS&W)에 대해서 실험을 통해 탈염기 성능 및 용량에 문제가 없는지 확인해야 한다.
(8) 황화철(FeS) 및 코크(Coke)
(가) 황화철은 황이 함유된 유체를 취급하는 공정 설비 내에서 배관 및 철제류 설비의 재질에서 철이 부식되면서 발생하는 것으로 공기에 노출되면 낮은 온도에서도 자연적으로 발화가 된다.
(나) 건조된 황화철은 공기에 순간적으로 노출될 경우에는 격렬하게 산화반응을 일으킬 수 있으나, 물과 혼합된 황화철 슬러지 형태는 수분이 완전히 건조될 때까지 산화가 지연되어 일반적인 산화시간이 길어지면서 설비 외부에서는 온도의 큰 변화가 조기에 발견되지 않을 수 있다.
(다) 황화철의 위험성은 정비보수 등 설비 개방시 외부 공기에 노출되면서 가장 빈번하게 나타날 수 있고, 특히 탑조류들의 맨홀 개방시 외부 공기의 유입으로 내부에서 자연발화되어 설비 손상 및 화재가 발생할 수 있다. 관련 위험성의 관리방법은 KOSHA Guide P-64 정유 및 석유화학 공정 내 황화철에 관한 안전관리 기술지침을 참조할 수 있다.
5.3 노출시 산업보건 측면 위험성
(1) 유기물질
(가) 메탄이나 에탄은 실내에 누출되면 산소 농도가 18 % 미만으로 낮아지면서 작업자에게 질식을 일으킬 수 있다. 따라서 밀폐공간 출입시 반드시 적정 보호구를 착용하여야 한다.
(나) 프로판이나 부탄은 흡입시 신경 계통에 문제를 일으킬 수 있다. 8시간 시간가중평균허용기준(Threshold limit value-Time weighted average, TLV-TWA)은 일반적으로 프로판이나 부탄이 600 ppm, 펜탄과 n-헵탄은 500 ppm, 납사는 100 ppm 정도이다.
(다) 모든 탄화수소류는 피부에 노출시 일정 시간 동안 계속해서 접촉되면 피부염을 일으킬 수 있다. 또한, 감압증류공정의 경유나 상압 잔사유가 계속해서 피부에 노출되면 발암물질로 작용될 수 있다.
(라) 원유와 정유 생산품에 포함된 모든 방향족 물질들은 발암물질이다.
(마) 부탄이나 프로판 같은 액화가스(Liquefied gas)가 피부에 노출되면 저온 화상을 일으킬 수 있다.
(바) 운전 중인 고온의 공정 설비에 직접 접촉 및 복사열에 노출되면 화상을 일으킬 수 있다.
(2) 무기물질
(가) 공정 설비의 보수나 검사를 위해 설비 개방시 내부의 먼지 등에 포함되어 밀폐공간 작업 등에 출입하는 작업자는 흡입과 섭취로 산업보건 측면 위험요인을 발생시킬 수 있으므로 반드시 적정 보호구를 착용하여야 한다.
(나) 황화철은 자연발화 위험성 외에 이산화황(SO2)을 발산하여 강한 자극성이 있으므로 노출시 인접 지역의 작업자들은 신속하게 대피해야 한다.
(다) 수은은 심각한 산업보건 문제가 증류탑의 오버헤드 부위 침전물 등에서 일으킬 수 있으므로, 탑조류의 기상 물질 샘플링을 통해 확인해야 한다.
5.4 유틸리티
유틸리티는 공정에서 생산을 위해 사용하는 필요한 지원 공정 및 물질을 말한다.
(1) 스팀(Steam)
(가) 스팀은 LP(Low pressure) 로 0.3 ~ 0.5 MPa, MP(Medium pressure) 로 1 MPa, HP (High pressure) 또는 초고압 스팀 (Superheated steam)으로 약 4 MPa 이상으로 구분할 수 있다.
(나) 초고온 스팀은 가열로(Heater)에서 공급되며, MP는 스팀 터빈이나 초고온 스팀을 감압하여 생산하고, LP는 MP를 감압하여 생산할 수 있다.
(다) 외부로 누출시 고온에 의한 작업자 화상, 보온 재질 내부로 누출된 탄화수소를 자연발화온도 이상으로 가열시켜서 점화를 발생시킬 수 있다.
(2) 용수(Water)
(가) 공정에서 배출되는 황화수소(H2S), 암모니아(NH3), 염화수소(HCl)에 의해 공정내 배관과 설비에 암모늄염(NH4Cl, NH4SH)이 형성되고, 막힘(Plugging)과 부식을 가중시키므로 공정 내 용수를 주입하여 암모늄염은 녹여내고, 황화수소, 암모니아, 염화수소 기체는 흡수시켜 해당 용수는 공정 외로 제거해야 한다. 암모늄염, 황화수소, 암모니아, 염화수소 기체를 흡수한 용수는 사우어 워터 스트리퍼 (Sour water stripper, SWS)에서 기체를 제거하게 된다.
(나) 만일 SWS 의 성능이 설계 한계치 미만으로 운전되면 독성가스 (황화수소, 암모니아, 염화수소 등)가 SWS 배출수 내 포함되어 있을 수 있다. 또한 SWS 배출수는 용존 무기염(Dissolved inorganic salts)을 가지고 있고, 이것이 눈에 접촉되거나, 분무되어 호흡기를 통해 흡입되거나, 피부를 통해 흡수될 수 있다.
(다) 탈염기에서 배출되는 용수는 상단 공정에서 주입된 용수보다 용존 무기염이 높은 농도를 가지고 있다. 만일 탈염기 용수의 액위 제어(Level control)가 정확하게 운전되지 않거나, 비 유화(De-emulsifying)를 위한 첨가제가 부족하면 용수내에 탄화수소가 포함될 수 있다.
(라) 탈염기의 배출수는 고온으로 취급되므로 탄화수소가 용수에 포함된 경우 대기 중으로 누출되면서 인화성 및 독성 증기운을 형성시킬 수 있다.
(마) CDU/VDU의 오버헤드 어큐뮬레이터(Overhead accumulator) / 환류 드럼(Reflux drum)에 축적되는 용수는 증류탑의 분리된 유체(Stripping stream)와 탈염기에서 비말동반된 수분의 혼합물이며, 암모늄염(Ammonium salt)과 같은 용존 무기염을 포함하고 있다. 따라서, 해당 유체는 정기적으로 운전원이 pH를 샘플링 검사하며, 취급시에는 보안경, 보안면과 불침투성 장갑을 착용해야 한다.
(3) 암모니아(Ammonia)
(가) 암모니아는 CDU/VDU 오버헤드에 무기산(Inorganic acid)을 중화시키기 위해 설계된 특정 CDU에 주입될 수 있다. 대부분의 공정은 암모니아보다 안전한 물질인 아민(Amine)으로 대체하여 사용한다.
(나) 무수 암모니아(Anhydrous ammonia)는 TLV 25ppm, STEL 35 ppm 으로 인화성과 독성을 모두 가지고 있는 물질로 외부로 누출이 되어서는 안된다. 암모니아가 누출될 경우에는 화학물질용 보호복과 자급식 호흡보호기(Self contained breathing apparatus, SCBA)를 착용하고 대응해야 한다.
(다) 일반적으로 암모니아는 이동식 트레일러로 하역을 통해 공정에 연결되어 공정내 저장탱크나 공정에 바로 연결하여 사용한다. 해당 지역에는 암모니아 누출을 대비하기 위한 중화처리 시설, 세안⋅세척시설과 필요시 양압 시설이 설치된 조정실 또는 운전원 대기실을 설치할 수 있다.
(4) 수처리용 화학물질
(가) 탈염기 유출수 처리와 냉각탑 수처리에 사용되는 많은 양의 화학물질이 외부 공급사를 통해 도입될 수 있다. 물질에 따라 인화성, 독성, 부식성을 가지고 있고, 이동식 용기를 통해 공급되거나, 트레일러를 통해 사업장 내 탱크로 하역되어 사용된다.
(나) 운전원들은 개별 화학물질 특성 이해를 위해 물질안전정보(Material safety data sheet, MSDS)를 인지 및 숙지해야 하며, 각 취급 방법 외 비상대응 조치와 적정 보호구 착용으로 상시 대응할 수 있어야 한다.
(다) 이동식 소형 용기를 설치 및 사용할 때 운반하는 지게차는 폭발위험지역 구분에 맞는 적정 방폭등급을 가진 지게차를 사용하고, 중량물 취급에 의한 작업자 상해를 주의해야 한다.
(5) 질소
(가) 공정 가동정지 및 정기보수시 공정 내 퍼지(Purge) 등에 사용되며, 계기류와 분석기 등에 정상 운전시 사용된다.
(나) 질소는 질식 위험성으로 공정 내에서 가장 위험성이 높은 기체로 밀폐공간 작업, 유해위험공간 내 출입 등에서 질식을 일으킬 수 있으므로 KOSHA Guide H-80 밀폐공간작업 프로그램 수립 및 시행에 관한 기술지침, KOSHA Guide X-68 밀폐공간 위험관리에 관한 기술지침, KOSHA Guide P-150 유해위험공간의 안전에 관한 기술지침을 적용한다.
(6) 방사능 물질
(가) 방사능 물질은 공정에서 액위를 측정하기 위해서 일부 사용할 수 있다. 방사능 물질과 감지기는 탑조류나 용기 측정 지점의 서로 반대편에 위치하고 감마선을 주사하여 내부 물질의 유량을 측정한다. 제작사가 해당 장비를 완전히 밀봉하고 개구부를 설치하여 주기적으로 검사 및 보수시 적용할 수 있도록 한다.
(나) 정확히 설치만 되면 정상 운전시에는 안전한 상태이며 검사, 보수 및 청소시 해당 물질 장비의 개구부가 반드시 밀봉하고, 방사능 물질이 제거 후에는 외부 저장소에 이송해야 한다. 또한, 방사능 물질 설치 및 저장 지역은 해당 지역 및 설비에 방사능 안전 표지를 게시해야 한다.
6. 공정 가동시작 및 가동정지 안전대책
6.1 인적 오류
(1) 가동정지 시에는 벤팅(Venting), 드레인(Drain) 및 퍼지(Purge)를 정확하게 실시한 후 개방하여 정기보수 중 인체사고 위험성을 줄일 수 있고, 공정 가동시에도 벤팅, 드레인 및 퍼지를 통한 산소 제거를 통해 공정안전 사고를 사전에 예방하는 것이 중요하다.
(2) 배관과 용기에서 드레인시 부식 물질과 내부 잔여물 등으로 막힐 수 있으며, 이것들은 가동 시작시 온도와 유량이 증가하면, 공정의 최저 지점(Low point)으로 이동되어 막히기도 한다. 또한, 가동 시작시 발생되는 막힘 증상으로 일정 용량을 개방하는 밸브에서 고형 응고물 형성 등이 심화될 수 있다.
(3) 특히, 드레인 중 급작스런 유체의 방출은 액상으로 튀거나 기상 누출로 이어져 밸브를 개방한 상태로 운전원이 바로 대피하거나, 상해를 입히기도 한다. 이것은 인화성 액체와 증기가 점화되기 전에 밸브 차단과 같은 조치를 위해 누출 지점에 접근하는 것을 예방할 수 있다.
(4) 정유공정은 많은 잠재 누출원들이 복잡하게 분포되어 있어 모든 플랜지, 배관 막음조치, 장비 플러그들이 정확하게 설치되어 누출이 불가하도록 가동전에 설치하고, 막아야 한다.
(5) 가동 정지 동안 개방되었던 벤트나 드레인들은 가동시작 전에 완전히 차단되었는지 확인해야 한다.
(6) 가열로는 전체 공장 가동 시작 중 가장 사고 발생 가능성이 높은 설비 중의 하나 이다. 대부분은 운전 절차나 안전조치 등을 따르지 않아 발생한다.
(7) 특히, 상압증류공정/감압증류공정의 전단에 위치한 가열로의 정기보수에서 가열로의 탈탄소 처리(Decoking)를 하고 스팀 등으로 퍼지 후 상압증류공정/감압증류공정과 연결된 배관의 맹판(Blind)을 공정 가동을 위해 제거하여 가열로 시운전으로 파일롯 버너가 점화되면서 상압증류공정/감압증류공정 내부의 탄화수소가 역류되어 화재⋅폭발이 발생한 사례가 있었다.
(8) 공정 가동시작 전에는 공정과 설비의 상태를 반드시 확인해야 한다. 공정 가동정지 중 많은 설비들이 교체 또는 수리되므로, 이 설비들을 가동 후에도 주기적으로 검사 및 추가적인 문제가 있었는지 확인해야 한다.
(9) 공정 가동시작 전 설비의 모든 용수가 드레인 되어야 한다. 특히, 가열로 같은 고온 설비에 수분이나 용수가 남아있으면 공정 가동시 증발되면서 과압이 순간적으로 발생할 수 있다.
6.2 설비 건전성 악화
(1) 공정 건설 및 설비 보수시 설비의 품질과 관리 절차를 제어해야 한다. 이때 잘못된 사항들은 공정이 가동될 때 반드시 공정 문제로 발생한다.
(2) 일부 부위는 부식이 심화되면서 가동정지 중 충분히 보완 및 제거되지 못하면 가동시 문제가 확대될 수 있다.
(3) 가장 일반적인 취약 지점은 변경으로 인한 ‘데드렉(Dead leg)’이 최초 설계와 달리 발생하는 것이다. 관련 배관 부위를 제거하여 데드렉을 피하며, 이러한 개선으로 배관에 맹판이 처리되면 프로젝트 비용과 설비 보수 일정이 추가 및 연장될 수 있다.
6.3 운전 변화에 따른 불안정한 공정 조건
(1) 공정 가동 시작과 정지는 배관과 공정에 기계적, 열적 스트레스를 줄 수 있다. 작은 실수나 변경도 이 단계에 더 큰 문제로 확대될 수 있다.
(2) 특히, 공정 건설 후 최초 가동시에는 정확한 운전 한계를 결정하기 어렵기 때문에 운전 조건을 변경 운영하면 불안정한 공정 조건이 발생할 수 있다.
6.4 드레인과 벤트의 캡 또는 플러그 미체결
(1) 공정 가동 중에는 모든 드레인과 벤트는 캡과 플러그를 체결하여 누출을 전단 밸브들와 함께 이중으로 방지해야 한다. 특히, 불안정한 공정 조건의 진동은 밸브가 열리면서 후단의 드레인이나 벤트에서 누출이 발생할 수 있다.
(2) 또한, 드레인을 위한 배관이 공정 내부 잔여물이나 건설 잔해 등으로 막히면 인접한 벤트나 다른 드레인의 개방으로 순간적인 대규모 분출이 발생할 수 있다.
6.5 잘못된 작업 및 운전
(1) 가동 시작 또는 중지시 상부 밸브나 설비 접근을 위한 접근로가 없으면, 운전원 추락이나 상해가 발생할 수 있다. (예. 접근로가 미설치된 고소 지역의 밸브 또는 설비를 운전하기 위해 운전원이 비정상적으로 접근하여 추락 발생 등)
(2) 잘못된 작업 및 운전을 예방하기 위해서는 공학적, 관리적으로 사전 원인을 제거해야 한다.
6.6 설비 노후화
(1) 일반적으로 정기보수 이후 공정은 건설 단계의 건전성을 회복할 수 있다. 장시간의 공정 운전은 설비의 부식 허용치 이상으로 공정의 노후화를 가속화시킬 수 있으므로 이에 대해 준비를 해야 한다.
(2) 최초 설계시 고려된 설비 보수 절차와 함께 상시 설비 건전성 악화 정도를 반영하여 KOSHA Guide P-119 노후설비에 관한 기술지침을 참조하여 설비 관리를 수행해야 한다.
6.7 공정 가동 중 정기보수 준비 및 수행
(1) 일반적으로 공정 가동 중 정기보수 준비를 시작하여 부분 실시할 때 작업 중에 위험물 누출 등이 발생할 수 있다.
(2) 또한, 비계 등 설비 보수를 위한 장비와 임시 설비를 설치하면 기존 운전을 방해하거나, 운전원 접근로 또는 이동 동선을 방해하여 예상치 못한 사고를 일으킬 수 있다.
(3) 협력사 작업자들이 상주하는 이동식 컨테이너는 시운전 또는 가동 중인 공정 지역이나 인접하면서 공정 화재⋅폭발 발생시 영향 범위에 포함될 수 있다.
6.8 설비 개방⋅철거
(1) 정기 보수시 많은 설비와 배관이 개방이나 철거되면서 내부 유체, 잔여물과 설비 내부 손상으로 인해 적정 설비관리 절차를 따르지 못하는 경우가 있다. 이런 경우에는 작업위험성평가와 작업허가서에 따라 위험성을 제어해야 한다.
(2) 설비 또는 배관을 개방⋅철거시에는 반드시 압력 및 내부 물질을 벤트, 드레인 및 퍼지 후 안전한 상태에서만 실시해야 한다. 이때 이러한 작업절차를 정의한 시스템 개방 (Line break) 절차를 적용해야 한다.
(3) 특히, 철거를 위한 용접 작업을 수행시에는 반드시 완전히 개방 후 잔존 가스 유무를 확인 수행토록 한다.
6.9 비정상⋅비상 가동정지 후 재가동
(1) 비정상 또는 비상 가동정지 후 공정 재가동은 일반 가동시작보다 더 높은 위험성을 가지고 있으며, 특히 계획되지 않은 가동정지는 바로 공정 가동 준비를 하면서 위험성이 가중될 수 있다. 이때 반드시 가동전 안전점검을 재실시하며, KOSHA Guide P-97 가동전 안전점검에 관한 기술지침을 따른다.
(2) 비정상 또는 비상 가동정지 중 설비에 손상을 줄 수 있다. 따라서, 재가동시에는 모든 공정 및 설비의 상태를 확인할 필요가 있다.
(3) 유틸리티 중 하나인 질소 등이 탄화수소로 인한 오염 가능성은 공정 내 원유 및 탄화수소의 유입이 될 수 있으므로 시스템의 건전성을 재확인해야 한다.
6.10 설비의 열적 손상
(1) 반복적인 가동 시작과 중지는 설비에 열적 손상을 주어 건전성이 낮아질 수 있다.
(2) 특히 플랜지 등의 볼트들은 열적 손상으로 시간에 따라 풀리면서 탄화수소 등이 외부로 누출될 수 있다.
7. 정상 운전 안전대책
7.1 인적 오류
(1) 밸브가 최초 설계의 닫힘⋅열림 상태와 반대인 경우 누출 등이 발생할 수 있다. 예를 들어 드레인 밸브가 개방시 배관 내 잔여물로 막힘 후 갑자기 유체가 배출되어 인체 상해가 발생할 수 있다.
(2) 또한, 운전 중 닫혀야 하는 밸브가 반대로 개방되면 공정 유체가 다른 공정이나 외부로 유입 및 누출될 수 있다.
(3) 핫 오일(Hot oil) 샘플링(Sampling)을 자연발화점 이상으로 취급하면 샘플링이나 드레인과 같이 대기에 순간적으로 노출되면 바로 점화되어 화상이나 화재가 발생할 수 있다.
(4) 공정 운전 모드의 변경이 급하게 실시되면 전체 공정에 영향을 주어 설비 이상 현상이 발생할 수 있다.
7.2 물질⋅에너지의 누출 (Material & energy loss of containment)
(1) 안전 측면에서 운전원의 역할은 공정 내부 물질이나 에너지가 누출 없이 정상적으로 운전을 할 수 있도록 감시 및 유지하는 것이다.
(2) 설계 오류나 부식⋅침식으로 설비가 파손되어 누출되는 것을 제외하면 피팅이나 전단 밸브 등이 진동이나 열변화로 풀리면서 누출될 수 있으므로 현장 순찰 및 확인을 해야 한다.
7.3 정리 정돈(Housekeeping)
(1) 공정에서는 정리 정돈이 기본이다. 플렉서블 호스(Flexible hose)나 각종 공정 지역 내 설비들은 바로 사용할 수 있어야 한다.
(2) 운전원들의 이동 및 공정 운전시 각종 비계 설치, 호스 배치, 설비 태그 등이 최초의도와 같이 정리 정돈해야 한다.
7.4 과압 발생
(1) 단일 제어 시스템 고장 또는 운전원 실수로 공정에 과압이 발생하여 탄화수소 등이 외부로 누출될 수 있다.
(2) 고온 공정으로 용수가 유입되면 순간적으로 기화되어 과압이 발생할 수 있다. 따라서, 원유 유조선에서 육상 원유 저장탱크로 이송시 최소한 48시간의 수분 분리 및 침전 시간을 규정하는 것을 권고한다.
(3) 탈염기는 물 슬러그(Water slugs)를 감소시키지만, 탈염기를 바이패스하는 경우 물 슬러그가 공정 내로 바로 유입되기도 한다.
(4) 또한, 과압은 유체를 이송할 때 밸브가 닫히면서 발생할 수 있다. 특히 고온 설비가 연결되어 있으면 온도로 인한 열팽창으로 가능성이 높아진다. 예를 들어 핫 오일 펌프를 시운전 중 가온(Warm-up)을 위한 리사이클링(Recycling)을 하면 펌프 후단에서 이송되는 핫 오일의 압력이 펌프 전단 설계보다 높아 전단 플렌지나 펌프 유입 배관에서 과압으로 인한 설비 손상과 누출이 발생할 수 있다.
7.5 저온 취성 및 수분 동결
(1) 동절기시 미사용 배관 또는 내부에 유체가 정체된 배관에서 수분이 모여 동절기나 저온 발생으로 동결되면서 부피가 팽창되어 설비, 배관, 밸브의 파손이 발생하여 누출되거나 동절기 후 파손된 배관 등이 해빙되어 물질이 누출될 수 있으므로, 액팽창밸브를 각 차단밸브마다 설치하거나 미사용 구획은 차단 후 드레인하여 예방한다.
(2) 또한 정유공정 외 인접 공정에서 액체 질소, 에틸렌, 프로필렌 등의 저온 취성이 가능한 유체가 일반 배관(탄소강 등)에 접촉하거나 흐르면서 동결 취성으로 파손될 수 있으므로 초저온 액체가 취급될 수 있는 설비, 배관재질에는 탄소강은 절대 사용해서는 안된다.
7.6 고온 손상
(1) 공정 온도가 너무 급속하게 상승하면 설비 손상이 발생할 수 있다. 일반적으로 공정 설비의 승온은 시간당 25℃ 로 제한하여 설비 건전성 및 내구성을 유지해야 한다.
(2) 외부 화재로 공정 설비의 밸브 등이 손상되어 누출될 수 있다. 또한, 롱 볼트 플랜지리스(Long bolt flangeless) 밸브는 3 인치 이상 외부 노출된 볼트에 열팽창이 발생하여 내부 유체가 누출될 수 있으므로 화염으로 직접 영향을 받을 수 있는 곳에 설치된 각 밸브 주위에는 금속 재질로 차단하는 설비를 설치해야 한다.
7.7 전력 중단
(1) 공정은 갑작스런 전력 중단에 대비한 비상전원 공급 시스템이 있다. 예로 가열로 등의 연료 공급 배관은 전력 중단시 공급 밸브가 자동으로 차단되지만, 플레어 이송 밸브는 수동으로 개방할 경우에는 오프 가스(Off gas)가 가열로 내부에서 점화되어 화재가 발생할 수 있으므로 플레어 이송 밸브는 자동으로 개방할 수 있도록 설치하거나, KOSHA Guide E-91 에너지 차단장치의 잠금 표지에 관한 기술지침에 따라 잠금 표지를 수동 밸브에 설치하여 식별해야 한다.
(2) 대기로 배출되는 안전밸브가 존재한다면 전력 공급 중단시 대기로 인화성 물질이 확산되며 화재⋅폭발 가능성도 있다. 이를 제어하기 위해서는 플레어와 같은 공정배출 시설(Process disposal system)으로 연결해야 한다.
7.8 인접 연결 공정 영향
(1) 화학 공정들은 서로 연결되어 한 공정의 문제는 다른 공정으로 이어질 수 있다. 원재료, 중간제품과 최종 생산품이 연결되었기 때문에 환경, 안전, 품질 및 생산 효율 등에 밀접한 관계가 있으므로 각 연결 공정에서는 상시 공정 운전 현황을 공유 및 의사소통해야 한다.
(2) 또한, 인접 공정의 화재⋅폭발 및 독성 물질 누출 발생시 동일 지역에 조정실이 위치한다면 전체 공정 운전에 영향을 줄 수 있으므로 공정 지역 내 건축물의 위험성 평가를 통해 건축물을 설계 및 건설해야 한다.
7.9 예비 설비(Standby equipment)의 건전성 유지
(1) 예비 설비는 운전 중인 설비와 동일한 건전성을 유지하고 자동 전환시 바로 가동할 수 있도록 관리해야 한다.
(2) 예비 펌프는 윤활유나 실링(Sealing) 등이 준비되지 않으면 전환이 어렵거나 전환 후 공정 운전이 어려울 수 있으므로 상시 가동이 될 수 있는 준비를 운전절차서에 따라 실시해야 한다.
7.10 임시 설비(Temporary equipment) 준비
(1) 설비 고장으로 임시 설비로 교체시 해당 지역의 공정 운전 조건이나 폭발위험지역 구분에 적정한 설비인지 반드시 확인해야 한다.
(2) 만일 관리가 되지 않은 설비로 대체되면 기존 설치 설비 운영보다 위험성이 높아 질 수 있으므로, 임시 설비를 설치시에는 변경관리를 통해 설계 적정성과 설비 건전성을 확인해야 한다.
8. 정기보수 위험성
8.1 시운전(Commissioning) 및 정상운전시 발생된 위험물 축적
(1) 정상운전이나 시운전 중 발생된 황화철과 같은 자연발화성 물질이 계속 적체되어 정기보수 중 공정 개방시 화재가 발생할 수 있으므로 KOSHA Guide P-64 정유 및 석유화학 공정 내 황화철에 관한 안전관리 기술지침을 적용하여 방지해야 한다.
(2) 특히, 정상 운전시 가열로의 대류 부분의 양압 조건은 가열로에 연결된 다른 공정으로 가열로의 유체가 흘러 들어갈 수 있다. 이것은 인접 공정에 부식을 일으킬 수 있으므로 KOSHA Guide P-168 화학설비의 부식 위험성평가에 관한 기술지침에 따라 도출된 설비 보존 프로그램으로 검사를 실시해야 한다.
8.2 과압 설비의 개방 중 물질⋅에너지 누출
(1) 가동정지 후 설비의 개방 또는 해체시 운전 압력이나 퍼지 등으로 질소가 공급되는 작업은 시스템 내부로 과압이 형성될 수 있고, 벤트 또는 드레인이 충분하지 않거나, 막힌 구간이 존재하면 배관 해체 또는 맨홀 개방 등에서 급작스런 압력의 방출이 발생할 수 있으므로 KOSHA Guide P-140 작업위험성평가에 관한 기술지침을 적용하여 사전에 위험성을 방지할 수 있어야 한다.
(2) 에너지나 물질의 누출은 정기보수를 준비하는 작업자들에게 인체 상해 및 화재⋅폭발을 일으킬 수 있으므로 정기보수 등의 시스템 개방시 가장 높은 빈도와 강도를 가진 것으로 시스템 개방 (Line break) 절차를 적용해야 한다.
8.3 유틸리티(Utility) 오염
(1) 전력(Electricity)을 제외하고 운전과 설비부서에서 필수 유틸리티로 간주하는 질소, 공기, 물은 정기보수시 가장 중요한 물질들로 항상 안전하고 오염이 되지 않아야 한다. 질소가 인화성 물질, 산소, 공기로 오염되어 퍼지 중 내부 폭발이 발생할 수 있으므로 상시 분리해서 설치해야 한다.
(2) 플랜트 공기(Plant air)나 계측 공기(Instrument air)에 질소를 예비로 연결하면 실내 압축기실 계기류나 밀폐공간 출입시 공급되는 공기에 질소가 포함되면서 질식이 가능하므로 제거해야 한다.
(3) 예로, 질소에 수소 배관이 연결되고 단일 밸브로만 차단하여 공정 내부에서 폭발하거나, 연속 이중 체크 밸브를 설치하였지만, 수소가 양압용 질소를 오염시켜 전기 패널 내부에서 폭발할 수도 있다.
8.4 고압 세척 (Water jetting) 위험성
(1) 30 ∼ 100 MPa 의 고압 세척 작업은 열교환기 등에서 인체 상해가 가능하다.
(2) 고압 세척 분사 기둥에 몸이 닿거나, 호스의 움직임에 걸려 전도될 수 있으므로, 관련 작업절차 적용과 함께 적정 보호구를 착용하고, 고압 세척 해당 작업자 외 안전 거리를 유지해야 한다.
8.5 공정의 부분 보수
(1) 상압증류공정/감압증류공정은 대규모 설비로 일부 구획이나 지역으로 한정하여 밀폐공간 및 화기 작업이 일어날 수 있다. 맹판과 밸브로 이중 잠금 등이 이루어지지 않으면 인화성 또는 질소가 운전 중인 공정에서 정기보수 작업 중인 구획으로 유입되어 질식 및 화재⋅폭발이 발생할 수 있다.
(2) 정기보수 중 공정에서 발생하는 작업은 동시성과 복잡성을 가지고 있으므로 작업허가서와 작업위험성평가 및 운전/작업절차 등으로 독립적인 제어가 필요하며, 이를 위한 정확한 P&ID(Piping and Instrumentation Diagram)를 기본으로 작업 계획과 허가를 검토해야 한다.
8.6 공정의 부분 재가동
(1) 공정의 부분 보수와 동일하게 부분 재가동은 기존 보수 중인 공정과 차단되고, 재가동되는 공정에서 인화성 물질이나 질소가 부분 보수 중인 지역에 인체 상해를 발생시킬 수 있다.
(2) 정기 보수 이후 공정의 재가동시에는 맹판 제거가 차단 순서와 반대 또는 올바른 제거 순서에 따라 이루어져야 한다.
8.7 내압 및 누출 검사
(1) 정기 보수 후 설비 변경 등으로 운전 압력 이상인 기압이나 수압 검사는 설비 변경이나 내구성이 약한 설비에서 과압 누출이 발생할 수 있다.
(2) 운전 압력 미만의 누출 검사는 0.2∼0.3 MPa 로 수행되며 누출시에는 인체 상해가 발생할 수 있다. 최대한 수압으로 검사하며 공정 특성상 불가하면 발생 가능 위험지역 내 모든 작업자들은 대피해야 한다.
9. 공정 설비 손상 및 고장 대책
각 공정 설비 및 고장에 대한 상세 사항은 각 관련 참조문헌을 추가 검토해야 한다.
9.1 탑조류, 용기 및 배관
(1) 부식
정유 공정 내에서 발생할 수 있는 부식은 기본적으로 API RP 571 Damage mechanisms affecting fixed equipment in the refining industry 에서 제시한 손상 원리(Damage mechanism)에 따라 적용된다. 부식은 전 공정에서 발생되며, 공정 설계시 재질 선정은 재질 전문가(Metallugy engineer)와 반드시 협의해야 한다.
(가) 염화암모늄 (Ammonium chloride; API RP 571 3.6)
1) 상압증류공정의 주요 탑조류 내부와 오버헤드 배관 컨덴서(Condenser)에서 염화수소와 암모니아의 결합으로 만들어진 염화암모늄에 의한 공식(Pitting corrosion)이 발생할 수 있다. 염화수소가 많을 경우 산부식(Acid corrosion)이 발생하며, 이를 완화시키기 위해 아민 등 pH 관리 물질을 주입시 조절이 잘되지 않으면 아민 (Amine) 부식이 발생할 수 있다.
2) 공정 운전시 다음과 같은 사항을 고려해야 한다.
- 허용 한도가 적정한 탈염기 세척 용수(저농도 암모니아)로 운전한다.
- 오버헤드 시스템의 필요량이 반영된 설계 유량으로 세척 용수를 적용한다.
- 필요한 액위에서 아민 첨가제가 얇은 층을 유지하는지 확인한다.
- 공정 내 염 승화(Salt sublimation) 온도를 인지하며, 온도는 염 종류의 부분압에 따라 달라질 수 있다.
(나) 염화수소 (Hydrochloric acid, HCl; API RP 571 3.37)
1) 용수의 응축수(Condensed water)가 첫 번째로 분리되는 상압증류공정 상압증류탑의 상부 시스템과 감압증류공정 이젝터(Ejector)/응축기(Condensator)에서 부식을 일으킬 수 있다.
2) 공정 운전시 다음과 같은 사항을 고려해야 한다.
- 저장탱크에서 원유의 응축수 분리와 배출을 극대화하며, 저장탱크에서 상압증류공정으로 이송되기 전에 최소 2일간의 침전 시간을 유지해야 한다.
- 적정 탈염기 운전을 확인해야 한다.
- 오버헤드 시스템의 필요량이 반영된 설계 유량으로 세척 용수를 적용한다.
- 요구되는 액위에서 중화와 아민의 얇은막을 형성시킨다.
- 운전원은 리플럭스 드럼(Reflux drum)/어큐물레이터 부트
(Accumulator boot)에 포집되는 오버헤드 용수의 pH를 정기적으로 모니터링하고, 운전 범위 이상이면 바로 조치해야 한다.
(다) 황화부식 (Sulfidation; API RP 571 3.61)
1) 원유에 포함된 황, 황화수소, 머캡탄(Mercaptan) 부식 반응으로 탄소강(Carbon steel)과 다른 합금에서 발생할 수 있으며, 공정의 고온 부위 (일반적으로 약 230℃ 이상)에서 발생한다.
2) 공급되는 원유에 황 함량이 높을수록 부식 가능성도 높아진다. 부식 예방 방법은 공정 조건과 운전 방법을 확인한 후 손상 원리(Damage
mechanism)를 분석하여 정확한 재질을 선택하여 설치한다. 특히, 최초 설계시 적용된 황화부식 방지를 위한 지시나 운전 방법은 준수해야 한다.
3) 고농도 황을 처리하는 고온 공정에 알루미늄으로 표면처리한 알로나이즈(Alonized) 저합금 금속이 있다면, 해당 금속을 제거할 때까지 운전 모니터링하고, 최대한 빨리 제거해야 한다.
4) 부식 발생시 설비 손상과 함께 황화철도 같이 발생될 수 있다. 황화철은 후단 공정 막힘 현상이나 설비 개방시 자연발화를 일으킬 수 있으므로 5.2 항을 적용한다.
(라) 나프텐산 (Naphthenic acid, NAC; API RP 571 3.46)
1) NAC를 포함한 원유가 상압증류공정/감압증류공정 공정의 고온에서 부식이 발생할 수 있다. 200℃ 이상의 상압증류공정/감압증류공정의 고온 부위와 난류가 강한 부위에서 대부분 발생한다. 특히 유체 속도가 빠른 배관이 취약하다.
2) 원유는 정상적으로 TAN(Total acid number)이 0.5 mg KOH/g를 초과할 때 부식 방지에 필요한 특별한 재질 선정을 고려해야 한다. 공정 엔지니어(Process engineer)와 생산관리자(Supply chain manager)는 TAN을 줄인 원유를 도입 및 혼합하여 NAC 취급이 허용되지 않은 공정의 부식 영향을 줄일 수 있다.
3) 고온인 NAC 억제제들은 사용이 가능하며, 산 부식을 최소화하기 위해 전체 공정 부식 모니터링 시스템을 사용할 수 있다. 투입 비율은 부식 비율과 연계하여 모니터링하여 결정한다.
4) 가열로 내부 튜브와 가열로 및 상압증류공정/감압증류공정 탑조류 사이의 연결 배관들이 특히 NAC에 취약하므로 KOSHA Guide P-168 화학설비의 부식 위험성평가에 관한 기술지침에 따라 재질 선정과 함께 설비 보존 프로그램으로 검사를 실시해야 한다.
(마) 습한 황화수소 손상 (Wet H2S damage; API RP 571 3.67)
1) 블리스터링(Blistering)과 크래킹(Cracking) 형태로 탄소강과 저합금강에서 발생할 수 있다. 황화철과 수소 원자를 생성하는 배관 내 스케일(Scale)에서 발생되는 산화철과 황화수소의 반응이 기본 부식 원리이다.
2) 수소 원자들은 배관 내부의 철이나 설비 내부 재질 쪽으로 확산되면서 확산 또는 통합되어 금속 내부에서 블리스터와 크래킹으로 형성된다.
3) 해당 부식 현상을 최소화하는 방법은 ‘오염된 철(Dirty steel)’을 피하고 공정 건설시 적정 재질을 선택하는 것부터 시작한다. 설비의 내부 코팅이 효과적이고, 모넬(Monel)을 상압증류공정 탑조류의 상부에 사용할 수 있다.
또한, 후열처리(Post weld heat treatment, PWHT)는 습한 황화수소손상을 줄이는데 효과적이다.
4) 운전원들은 용수의 pH 검사를 하며, 운전 한계 이상인 경우 생산 책임자에게 보고 및 조치해야 한다.
5) 고농도 황화수소 유체의 샘플링은 위험하므로 안전작업절차에 따라 수행해야 한다. 폐쇄식 샘플링 시스템(Closed-loop sampling
system)이나 자급식 호흡보호구를 착용 후 수행해야 한다.
(바) 염기성 응력 부식 (Caustic stress corrosion cracking; API RP 571 3.15)
1) 탄소강, 저합금강 그리고 300 계열 스테인리스 스틸이 수산화나트륨(NaOH) 또는 수산화칼륨(KOH)에 노출되면 발생된다.
2) 제작 공정에서 생성되는 응력을 해소하기 위해 621℃까지 온도를 올리는 후열처리를 하여 탄소강 배관과 용기에서 크랭킹이 발생되는 것을 방지한다.
스팀 트레이싱 (Steam tracing)을 설치한 후열처리가 되지 않은 탄소강과 스팀 방출시 특별한 주의가 필요하다.
(2) 부적절한 설계와 건설
(가) 데드렉(Dead leg) 내 부식
1) 배관 내 데드렉은 최초 공정 설계시에는 일반적으로 발견하기 어렵다.
최초에는 흐름이 정체된 구간, 제어 밸브(Control valve) 또는 열교환기들 주위의 바이패스 구간에서 주 공정 배관으로 자유롭게 드레인될 수 있도록 설계된다. 또한, 변경으로 발생된 데드렉은 기존 배관이 제거되지 않고, 추가적으로 배관을 설치하면서 형성될 수 있다.
2) 일부 데드렉들은 배관들이 간헐적으로 사용되면서 형성될 수 있다. 이런 환경에서는 재질을 상향하는 측면에서 이종 재질 (Exotic metallurgy)을 사용하거나, 정상적으로 운전시 전면 차단 후 가스 오일(Gas oil) 등으로 비정기적인 플러싱(Flushing)이 필요하다.
3) 데드렉에는 설비 하부 부식(Under deposit corrosion, UDC)을 급속하게 일으킬 수 있는 슬러지(Sludge)와 화학물질이 축적될 수 있다.
(나) 최초 건설시 부적절한 재질
1) 예상하지 못한 많은 주요 사고들은 잘못된 건설 재질로부터 발생한다. 특히, 부식에 의한 고장이나 손상은 최초 중요성이 낮은 구간에서 장시간에 걸쳐 발생할 수 있다. (부적절한 물질의 사용은 부식에 의한 손상 시간을 단축시킨다.) 또한,이종 물질 간 용접 설치시에도 가능하다.
2) 따라서, 모든 사업장은 기존과 신규 설비에 대한 재질 적정성 확인 프로그램으로 관리해야 한다.
(다) 부적절한 지지대
1) 공정 진동, 용접 부위에 과도한 스트레스, 지지대 이탈등을 발생시키는 부적절한 지지대가 원인이 될 수 있다.
2) 주요 원인은 설계 오류, 용접 불량, 지지대 피로도 상승에 의한 파손 등이다.
(3) 탑조류와 용기의 과충전
(가) 공학적 접근 검토
1) 상압증류공정/감압증류공정의 탑조류와 용기(Vessel)에서는 빈번한 액위 조절의 오류로 인해 과충전이 발생할 수 있다. 이것은 다양한 변수로 인해 발생할 수 있으며, 예로 원재료(Raw material) 증류 다양성, 잔사유 스트리핑 트레이 막힘, 액위 측정 장비 노즐의 막힘, 액위기 불량 또는 고장 등이다.
2) 과충전되는 탑조류/용기는 해당 설비의 안전밸브가 대기로만 연결되면 탄화수소들이 대기로 배출될 수 있다. 모든 탑조류에는 정확한 액위 측정 계기(Level transmitter)와 인터락(Interlock) 외 추가 액위 계기를 설치하는 것을 권고한다.
3) 과충전된 탑조류와 용기들의 지지대 기반과 용기 스커트(Skirt)는 액체 과충전으로 과부하가 발생할 수 있다.
(나) 탑조류 과충전 방지 기준
1) 대기로 방출되는 상압 안전밸브(Atmospheric relief valve, ARV)를 가진 모든 탑조류와 용기들은 두 개 이상의 분리된 액위 계기류를 가지고 있어야 한다.
2) 플레어로 연결된 안전밸브를 가진 탑조류와 용기들은 두 개 이상의 분리된 액위 계기류의 필요성을 공정위험성평가시 결정한다.
3) 모든 탑조류와 용기들의 공정 변수들은 중요 알람(Critical alarm)으로 관리하며, 중요 알람(Critical alarm)은 신뢰성을 유지하고, 바이패스 등을 하지 말아야 한다.
4) 공정위험성평가, 방호계층분석(Layer of protection analysis, LOPA)을 통해 모든 탑조류, 용기들에 추가적인 계기류 설치, 높은 신뢰성의 계기류와 인터락을 설치한다. 필요시 안전무결성 등급(Safety integrity level, SIL)을 적용하여 신뢰성을 유지할 수 있도록 한다. 액위 계기류의 선호도는 레이더, 방사능, 차압 자기 커플(Magnetic couple) 순이다.
5) 신규 탑조류들은 분리된 액위 계기류 노즐로 설치하고, 보완할 경우에는 과거 막힘(Plugging) 이력을 고려하여 개별 노즐로 분리하여 설치하는 것을 검토한다.
(4) 탑조류 내부 범람 (Flooding)
(가) 트레이(Tray) 범람 종류 및 특징
범람은 증류탑 내부에서 액상 유체가 과도하게 축적되는 현상으로 설비 손상이 일어나 탑조류 외부나 타 설비로 역류나 누출이 발생할 수 있다.
1) 스프레이 비말동반 범람(Spray entrainment flooding)
하단 트레이로 이동하는 액상 유체가 상단 트레이에서 축적되는 현상이다.
2) 프로스 비말동반 범람 (Froth entrainment flooding)
트레이 증기 속도가 증가하면 프로스(거품) 형태로 변환되어 스프레이 비말동반 범람이 발생하는 현상이다.
3) 다운커머 백업 범람 (Downcomer backup flooding)
다운커머에서 액상 유체가 축적되면서 트레이 간격을 초과하여 상단 트레이에 축적되면서 범람이 발생하는 현상이다.
4) 다운커머 쵸크 범람 (Downcomer chock flooding)
액상 유량이 증가하면 다운커머에서의 유속은 증가하고, 이 유속이 일정 수준을 벗어나게 되면 다운커머에서의 마찰 손실이 크게 증가하여 트레이 하단으로 액체가 내려가지 못하면서 트레이에서 액체가 축적되면서 범람이 발생하는 현상이다.
(나) 탑조류 범람 사전 감지
범람은 탑조류에서 유체가 축적되면서 최악의 경우에는 탑조류 전체가 액체로 채워질 수 있고, 이것은 과충전과 같은 현상이 일어날 수 있다. 따라서, 사전에 감지 및 사전 조치가 필요하다.
1) 탑조류 차압의 기존 값과 차이 감지
2) 탑조류 차압의 급격한 증가
3) 탑조류 하부 액상 유체의 급격한 손실
4) 탑조류 상부 트레이의 급격한 비말동반 현상 증가
5) 분별 증류 효율 상실로 온도 프로파일(Profile) 변화 등
9.2 탈염기 (Desalter)
(1) 공정안전에 영향을 주는 심각한 운전 변수(Parameter)
(가) 중요한 운전변수들은 공정 관리자와 운전원들이 반드시 이해해야 하며, 운전원은 주기적으로 유입되는 혼합된 원유들과 탈염된 원유에서 염분, 고형물, 그리고 수분 함유량을 모니터링해야 한다. 추가적인 매개변수들은 다음과 같다.
1) 원유의 염분 성분
2) 고형물과 원유 운반선이나 원유 탱크 바닥 퇴적물 및 수분(Bottom sediment and water, BS&W)
3) 수질 및 용수 주입량
4) 혼합 밸브 (Mixing valve) 압력 저하
5) 탈염용 화학물질 주입 형태와 유량
6) 계통 전압(Grid voltage)과 전류
7) 탈염기 온도와 압력
8) 염수 pH 와 염수/원유 경계면 수위
9) 원유로 주입되는 슬랍오일(Slop oil)용량
(나) 고온 염수의 샘플링은 샘플 쿨러(Sample cooler)를 사용하고, 전면 보호구와 불침투성 장갑을 착용해야 한다.
(2) 방출수의 수질
(가) 방출수 수질은 정기적으로 모니터링해야 한다.
(나) 운전원들이 공정 변수로 모니터링이 정확하지 않을 경우 사이트 글라스(Sight glass)로 방출수 색깔을 모니터링할 수 있다. 사이트 글라스는 투명한 운모재질의 부식 방지 필름을 안쪽 표면에 부착해야 한다.
(3) 용수 공급
(가) 탈염기에 공급되는 용수는 상압 탱크나 대용량 사업장 내에 위치한 저수지 등을 통해 공급할 수 있다.
(나) 탈염기 용수 공급 펌프 고장이나 체크 밸브 고장으로 역류가 발생하면 용수 공급 수원으로 원유가 유입되어 전체 용수 오염이나 수원 상압 탱크 벤트로 원유 유출, 탱크 범람에 의한 원유 누출이 발생할 수 있다.
(4) 전극 전력 공급
(가) 고압 전력 공급 변압기와 관련 전선, 전극 등은 가동 조건에 대해서 정확한 정보 교류 및 설비관리가 필요하다.
(나) 이에 대해서는 KOSHA Guide E-91 에너지 차단장치의 잠금⋅표지에 관한 기술지침에 따라 관리가 되어야 한다.
9.3 가열로 (Fired heater)
(1) 공정안전에 영향을 주는 심각한 운전 변수
(가) 가열로는 상압증류공정/감압증류공정의 열원으로 공정 전 범위에 영향을 줄 수 있다.
(나) 가열로 유체의 최대 온도는 가열로 운전 중 가장 중요한 변수이다. 운전 한계를 초과한 온도로 가열시 코크(Coke) 형성 비율을 상승시키고, 가열로 튜브 내에서 분해 가스(Cracked gas)의 생성이 될 수 있다.
(다) 튜브 코킹(Coking)의 영향을 받는 인자들은 공정안전과 효율적인 운전을 위해 중요하다. 가열로를 담당하는 운전원은 이러한 운전 변수들을 포함하여 확인해야 한다.
(라) 공정 관리자들과 운전원은 가열로 튜브에서 허용하는 최대 외면 온도를 반드시 이해해야 한다. 정상 운전시에는 표면 열전대(Surface thermocouple)로 모니터링하며, 고장이 발생할 경우에는 정기보수 기간 동안 보수가 가능하다.
(마) 개별 표면 열전대가 고장이 나면 가열로 전체 온도 측정계기로 파악할 수 있으며, 이때 가열로 전체 표면 온도는 가열로 튜브 유량 측정계기, 제어 밸브의 오류 또는 오작동과 가열로 튜브 내 유량 감소를 간접적으로 지시할 수 있다.
(바) 가열로 전체 온도 측정 중 지시된 튜브 표면 온도 이상 현상은 조사하여 원인을 확인해야 하며, 만일 유량 감소 등이 확인된다면 바로 가동정지해야 한다. 이때 튜브 표면 온도는 적외선 열화상측정기로 측정할 수 있다.
(사) 원유 도입량이 설계치의 60% 미만으로 감소하면 튜브 내부 속도를 유지하기 위해 탄화수소 회수 시스템(Recycle hydrocarbon stream)을 적용하거나 스팀을 주입한다. 이런 조치가 적용되지 않으면 튜브들의 내부 표면에는 코크가 형성되어 유체와 튜브 내부 금속 재질이 열적으로 절연된다. 이때 튜브 벽이 과열되며 부식이 급속화되고, 외부 표면은 스케일이 쌓이면서 튜브 벽이 부풀어 오르
는 현상(Bulging)이 발생되어 손상이 발생될 수 있다.
(아) 본질적으로 가열로의 운전 범위는 가열로 전문가가 검사 및 확인되고, 이 결과는 공정 관리자와 운전원들이 이해해야 한다.
(2) 연료 주입 시설 차단
(가) 튜브 유량이 갑자기 감소되면 주 연료 공급 시스템(Main fuel injection system)은 바로 차단되며, 파일럿 시스템은 시운전 (Commissioning) 상태로 대기한다.
(나) 가열로 내부에는 점화 설비 외에는 연료가 주입되면 안되고, 공급 배관은 이중으로 차단하고, 점화 전에 연료가 주입되는 것을 모니터링 하며, 운전 중 점화없이 연료만 주입되지 않도록 해야 한다. 관련하여 KOSHA Guide P-66 연소소각법에 의한 휘발성 유기화합물(VOC) 처리설비의 기술지침에서 제시한 연료 배관의 긴급차단밸브 설치 사항을 참조한다.
(다) 가열로 내부 점화시 내부 잔여 인화성 기체에 의한 폭발을 제어하기 위해서는 KOSHA Guide P-123 공업용 가열로의 안전에 관한 기술지침을 적용하여 제어한다.
9.4 회전기기 (Rotating equipment)
(1) 부식
(가) 탑조류, 용기, 배관과 유사한 부식 현상이 펌프 케이싱 등에서 스크류 플러그(Screw plug) 부식과 같이 발생될 수 있다.
(나) 회전기기의 재질 선정은 회전기기 엔지니어의 역할로 재료 또는 재질 엔지니어의 검토를 받지 않는 경우가 많아서 재질 선정에 부적절한 경우가 발생할 수 있다. 따라서, 재질 선정시 유체가 부식성 물질일 경우에는 재료 또는 재질 엔지니어의 검토 및 기존 부식 사고 이후에는 정확한 손상 원인을 파악하여 재질을 선정해야 한다.
(2) 진동
(가) 지지되지 않은 설비나 장비의 소구경 배관에 연결된 압력계 등은 진동으로 손상이 가능하다. 손상은 다음과 같이 조건에서 악화될 수 있다.
1) 설비 자체의 진동 사이클을 가진 설비(예. 왕복동식 압축기)
2) 한계 속도(RPM) 이상으로 운전하는 설비
3) 설비 자체 압력 증가만큼 과압될 수 있는 후단 연결 배관과 차단 밸브
(나) 공정 가혹도가 높은 탄화수소 또는 중요 유틸리티를 취급하는 절연되지 않은 압축기 피팅류 등의 소구경의 배관 연결부는 진동에 취약하다. 일반적으로 벤더 패키지(Vendor package) 내부 등으로 압축기의 씰 오일 리턴 배관(Seal oil return line) 등이 산업 규격(예. API, ASME 등)을 만족하지 않을 수 있다.
(다) 설비 재질이 운전 조건에 맞지 않으면, 부식과 진동이 동시에 발생하여 대량 누출까지 발생할 수 있다.
(3) 메커니컬 씰(Mechanical seals)과 씰 시스템(Seal system)
(가) 메커니컬 씰 시스템 고장
API (American petroleum institute) 참고 문헌에서 적정 씰 플랜(Seal plan)을 확인하며, 메커니컬 씰을 이중 설계로 설계할 수 있다.
(나) 베어링(Bearing) 손상 또는 고장
1) 모든 회전기기 씰의 가동은 회전기기들의 원활한 구동에 따른다. 베어링 고장은 씰의 파손으로 이어져 인화성 물질 누출까지 발생할 수 있다.
2) 가동 중인 펌프에서 인화성 물질이 누출되면 자연발화나 정전기로 점화될 수 있다. 베어링이 손상 등으로 조정 불량에 따라 회전체와 고정설비 사이에서 마찰열이 발생하여 점화 에너지를 발생시킨다.
(다) 씰 오일 시스템 적용
1) 메커니컬 씰은 저온의 깨끗한 유체가 씰 접촉면에 공급되어야 한다. 펌프의 주 공급 배관에서 냉각기(Cooler)와 고체 분진을 제거하는 작은 집진기로 구성된 씰 어셈블리까지 연결되는 기본 씰 오일 시스템을 가지고 있어야 한다.
2) 일부 메커니컬 씰은 외부 장치로부터 씰 오일을 공급하는 시스템이설치될 수 있다. 이런 장치는 중요한 안전 시스템(Critical safety system)
으로 고려해야 한다. 외부 씰 오일 공급 시스템에 고장이 발생하면 펌프는 바로 가동정지해야 한다.
3) 텐덤 씰(Tandem seal), 더블 메커니컬 씰(Double mechanical seal)과 같은 씰 오일 시스템도 동일하게 중요한 안전 시스템으로 적용해야 한다.
(라) 비상시 가동 중인 펌프 차단
1) 비상시 가동 중인 펌프는 바로 차단이 되도록 펌프 자체 가동 정지 버튼과 차단 밸브가 설치되어야 한다.
2) 인화성이나 독성물질을 취급하는 펌프는 해당 지역과 조정실 등의 외부에서 가동정지할 수 있도록 설계하며, 원거리 가동정지는 15 ~ 30m
이상 이격된 지역에서 가능하도록 설계하는 것을 권고한다.
(마) 씰 파손시 화재 피해 최소화
1) 씰이 파손되면 회전기기 인접 지역과 상부에 누출 후 화재가 발생할 수 있다.
화재로 보호되지 않은 계전 시설과 전선관들은 취약하다. 이러한 전선관들과 인접 설비들은 물리적인 방법을 포함하여 보호를 해야 한다.
2) 회전기기 상부에 있는 설비들은 모두 이설해야 한다. 단, 이것은 기존 시설에서 불가하면 추가적인 보완이 필요하다.
3) 인접 지역에 설치되는 계기류와 전선관들은 본질적으로 화재에 대비하도록 불연 또는 난연으로 설계하여 화재에 대한 영향을 최소화시킨다.
4) 화재 보호가 되지 않은 전선관 주위는 내화처리를 실시한다. 상시 화재로 부터 보호되며, 설비 관리와 점검시에만 해체되거나, 최대한 단시간에 완료할 수 있도록 해야한다.
(바) 상시 모니터링
1) 회전기기에는 중요한 안전 계기와 각종 알람 및 인터락은 운전원들과 시스템을 통해 상시 모니터링되어야 한다.
2) 씰 운전 조건과 씰링하는 유체의 공급, 스팀 냉각 등의 상태도 모니터링해야 한다.
(사) 메커니컬 씰 설계
메커니컬 씰은 일반적으로 중요한 안전 시스템으로 고려되며, 이중 차단 장치를 가지고 있다. 예를 들어 이중 메커니컬 씰과 이중 차단 씰 등이다. 다음의 경우에는 이중 메커니컬 씰이나 이에 상응하는 장비가 설치되어야 한다.
1) 취급 물질을 자연발화온도 이상으로 운전하는 고온 펌프
2) LPG 펌프
3) 진공 이하 압력에서 유입하는 펌프들
4) 고농도 황화수소를 이송하며 누출시 1,000 ppm 이상을 배출될 수 있는 펌프들
(4) 커플링 (Coupling)
(가) 커플링은 설계와 설치시 복잡한 여러 부품들의 조립품이다.
(나) 정렬 불량(Misalignment)은 커플링의 설치가 정확하지 않거나, 드라이버(Driver) 또는 추진체(Driven equipment)가 시간이 지나면서 얼라이먼트를 벗어난 경우 적정 조치가 실시되지 않으면 발생할 수 있다. 해당 개별 부품들이 적정하게 설치되었다면 발생하지 않는다. 일반적으로 커플링의 손상이나 고장은 위험물의 대량 누출로 이어질 수 있다.
(다) 커플링은 회전기기의 일부 부품들이 부분 변경되면 한계 이상의 속도 이상으로 운전시 변경 부위가 약화될 수 있다.
9.5 열교환기
(1) 공정안전에 영향을 주는 심각한 운전 변수(Parameter)
(가) 콘덴서, 쿨러, 리보일러(Reboiler)를 포함한 상압증류공정/감압증류공정 내 열교환기들은 공정에서 에너지 효율 측면으로 중요하다.
(나) 열교환기는 최종 생산품으로부터 원재료에 열의 회수 또는 이동을 수행하고, 외부 열원의 공급되는 열(Heat)의 양을 최소화하는 것이다. 열교환기는 생산품을 냉각하는 공기 또는 물에 의한 열손실의 양도 제어해야 한다.
(다) 열교환기의 운전과 성능(Performance)을 제어하는 인자들은 다음과 같다.
1) 유체 종류, 염도, 침전물, 오염물질, 탈염 성능, 튜브 내부 속도, 열교환기 설계, 부식, 온도, 용수 측 전처리 적정성 등이다.
2) 운전원이 원유를 추가적으로 처리하지 않으면, 낮은 온도에서 부식과 파울링(Fouling)이 나타날 수 있다.
(2) 파울링(Fouling)
(가) 열교환기 성능과 파울링은 정기적으로 모니터해야 한다. 설계상 필요한 용량의 열 이동을 수행하지 못하면 가열로 관련 설비의 과부하를 줄 수 있고, 공정효율과 안전 운전을 방해하며, 최종적으로 설비 고장이나 파손으로 이어질 수 있으므로 다음과 같은 사항을 준수해야 한다.
1) 열교환기 튜브 속도는 일반적으로 1.0 ∼ 3.0 m/s 로 유지하며, 관련 엔지니어링 설계 사항에 따른다.
2) 열교환기의 바이패싱(Bypassing)과 유속이 감소되는 스로틀링(Throttling)을 할 경우 파울링이 증가될 수 있다. 또한 냉각수는 용수 측의 파울링을 방지하기 위해 50℃ 미만으로 유지해야 한다.
(나) 운전 중 주기적인 세척 작업 (라이트 사이클 오일과 다른 용매를 사용), 운전외 고압 세척, 운전 중 화학물질 투입 등과 같이 열교환기들 내부에서 파울링을 제한할 수 있는 다양한 방법들을 사용한다. 냉각 용수 열교환기들은 주기적으로 역 플러싱(Back flushing)을 할 수도 있다.
(다) 파울링은 다음과 같은 취약 지점을 고려하여 방지해야 한다.
1) 염화암모늄염(Ammonium chloride salts)이 쌓일 수 있는 다양한 혼합물이 있는 오버헤드 배관들
2) 아스팔텐(Asphaltene), 코크가 쌓일 수 있는 잔사유⋅원유 열교환기들로 양압 상태에서 차단, 배관 세척 오일 적용 및 드레인 시스템은 개별 또는 두 개 이상의 열교환기들을 고압 세척시 안전하게 바이패스하고 차단해야 한다. 특히, 고압 세척은 핀팬(Fin fan)에 쉽게 손상을 줄 수
있기 때문에 핀팬의 외면 청소시에는 사용하지 않는다.
3) 운전원들은 열교환기 대기 개방시 열교환기 내부에 쌓인 황화철 스케일은 코크 침전물의 점화 가능성을 인지해야 한다. 세척 작업 중 발생된 폐기물들을 건조시켜서는 안된다.
4) 투관형(Shell and tube) 타입 냉각기와 콘덴서들에 대한 역 플러싱(Back flushing)은 온수로 파울링을 발생되는 곳에 사용할 수 있다. 따라서 튜브측에 탄산칼슘 침전물(Calcium carbonate deposition)로부터 파울링 발생 예방을 위해 배출수 온도는 50℃를 초과해서는 안된다.
5) 토양 및 수질 오염 예방을 위해 연약 지반으로 역 플러싱된 용수의 방출을 금지하며, 폐수처리장으로 이송해야 한다.
6) 이종 재질로 제작된 열교환기들의 세척시에는 손상 예방이 필요하다.
고압 세척이나 금속 막대기와 같은 도구로 세척되면 일부 손상된 티탄늄 튜브가 재가동 중 수소 취성(Embrittlement)으로 파손될 수 있다.
[첨부자료] 정유시설의 안전 운영에 관한 일반적인 위험관리에 대한 기술지침(P-174-2021)
'산업안전' 카테고리의 다른 글
산화성 액체 및 고체의 안전관리에 관한 기술지침(P-45-2012) (0) | 2022.09.28 |
---|---|
용해로의 설치 및 유지보수에 관한 기술지침(P-143-2014) (0) | 2022.09.26 |
화학설비의 부식 관리문서 개발에 관한 기술지침(P-175-2021) (0) | 2022.09.24 |
이동식 사다리의 제작과 사용에 관한 기술지침(G-130-2020) (0) | 2022.09.22 |
전기설비 설치상의 안전에 관한 기술지침(E-85-2017) (1) | 2022.09.21 |